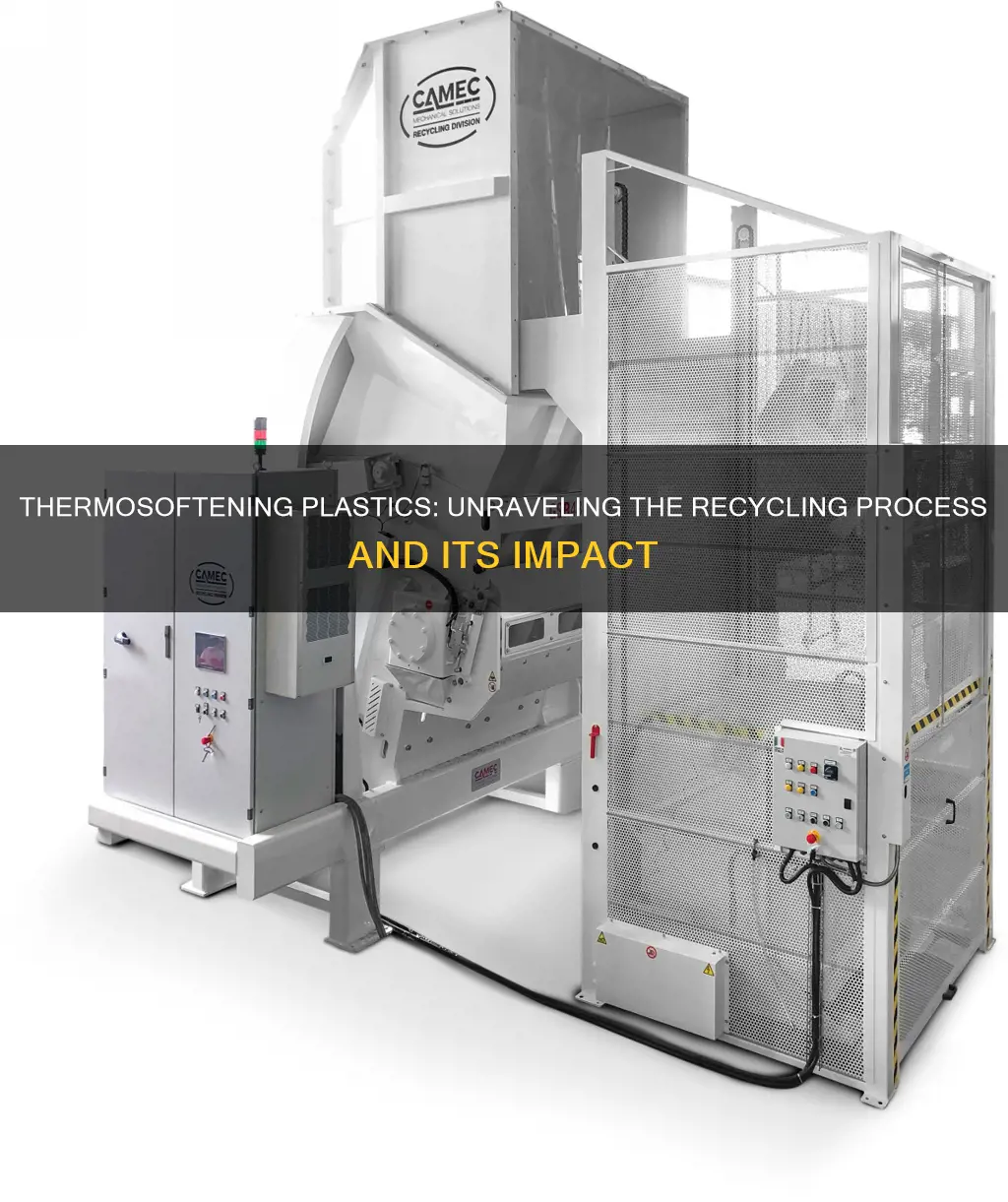
Thermosoftening plastics, also known as amorphous plastics, are a type of plastic that becomes soft and pliable when heated and hardens when cooled. Recycling these materials is crucial for environmental sustainability. The process begins with collecting and sorting the thermosoftening plastics, which are then shredded or granulated to reduce their size. Next, the plastic is cleaned to remove any contaminants, ensuring it is free from impurities. The cleaned plastic is then melted and molded into new products or used as a raw material for various applications. This recycling method helps reduce waste and promotes the circular economy by giving new life to these unique plastics.
What You'll Learn
- Collection and Sorting: Separate plastics by type and color for efficient recycling
- Shredding and Granulation: Break down plastics into small pieces for easier processing
- Chemical Treatment: Use solvents or catalysts to break polymer chains and recycle
- Re-melting and Molding: Melt recycled plastics and reshape them into new products
- Quality Control: Inspect recycled plastics for purity and consistency before reuse
Collection and Sorting: Separate plastics by type and color for efficient recycling
The process of recycling thermosoftening plastics begins with a crucial step: collection and sorting. This initial phase is essential as it sets the foundation for efficient recycling and ensures the quality of the recycled material. The goal is to separate plastics into different types and colors, a process that requires careful attention to detail.
Collection points are established in various locations, such as recycling centers, waste management facilities, and even directly from consumers. These points are designed to capture a wide range of plastic waste, including those commonly used in packaging, containers, and various household items. It is important to encourage proper waste segregation at the source, where individuals and businesses can start by identifying the type of plastic they are dealing with. Common types include PET (polyethylene terephthalate), HDPE (high-density polyethylene), PVC (polyvinyl chloride), LDPE (low-density polyethylene), and PP (polypropylene), each with unique properties and applications.
Once collected, the plastic waste undergoes a sorting process. This can be done manually or through automated systems. Manual sorting involves trained personnel who visually inspect and separate the plastics based on their type and color. For instance, PET bottles are typically clear or slightly tinted, while HDPE containers are often translucent. PVC pipes or profiles might be identified by their rigidity and color. This manual process requires expertise and precision to ensure accurate sorting.
Automated sorting systems utilize advanced technologies such as near-infrared (NIR) spectroscopy and optical scanners. These machines can identify and separate plastics based on their unique molecular structures and colors. NIR spectroscopy can detect the type of plastic by analyzing its infrared spectrum, while optical scanners use cameras to identify colors and shapes. These automated methods increase efficiency and accuracy, especially when dealing with large volumes of waste.
Proper sorting by type and color is crucial because it allows for the development of specific recycling streams. Different types of plastics have varying chemical compositions and melting points, which influence their recyclability and the quality of the recycled material. For example, PET and HDPE are widely recycled and can be used to create new containers, while PVC might be more challenging to recycle due to its chemical properties. Sorting by color is also important as it can affect the appearance and functionality of the recycled product. Clear PET, for instance, can be recycled into clear containers, while colored PET might be used for different applications.
Recycling Plastic: Environmental Friend or Foe?
You may want to see also
Shredding and Granulation: Break down plastics into small pieces for easier processing
The process of recycling thermosoftening plastics begins with the collection and sorting of these materials, which are often used in packaging, containers, and various consumer products. Once sorted, the plastics are prepared for recycling by a method known as shredding and granulation. This process is crucial as it transforms large, bulky plastic items into smaller, more manageable pieces, making them easier to handle and process further.
Shredding is the initial step, where the plastics are fed into a shredding machine. These machines are designed to cut and tear the plastic materials into smaller fragments. The shredding process can vary depending on the type of plastic and the desired outcome. For instance, some shredders use rotating blades to cut the plastics into thin strips, while others employ a more aggressive approach with heavy-duty blades to create smaller, more uniform pieces. The goal is to reduce the size of the plastic items significantly, making them less bulky and more suitable for the next stage of recycling.
After shredding, the plastic fragments are then conveyed to the granulation process. Granulation involves further breaking down the shredded plastic into even smaller particles, typically in the form of granules or pellets. This is achieved through a process called 'pelletizing', where the shredded plastic is heated and then extruded through a die to create small, uniform pellets. The heat applied during granulation helps to melt and fuse the plastic fibers, ensuring a strong and consistent final product.
The granulation process offers several advantages. Firstly, it allows for the creation of a standardized product, making it easier to transport and store. These plastic granules can then be used as raw materials for manufacturing new products, such as furniture, automotive parts, or even new packaging. Secondly, granulation helps to remove any contaminants or impurities that may have been present in the original plastic items, ensuring a higher quality end product. This process is a critical step in the recycling chain, as it prepares the plastic for further processing and reuse.
In summary, shredding and granulation are essential techniques in the recycling of thermosoftening plastics. By reducing the size of the plastic materials, these processes make it easier to handle and process them further. The resulting granules can then be utilized in various industries, contributing to a more sustainable approach to plastic waste management. This method of recycling is a vital part of the circular economy, ensuring that valuable resources are recovered and reused.
Unraveling the Mystery: Can Plastic Silverware Be Recycled?
You may want to see also
Chemical Treatment: Use solvents or catalysts to break polymer chains and recycle
Chemical treatment is a crucial process in recycling thermosoftening plastics, which are known for their ability to soften and flow when heated, making them ideal for various applications but also challenging to recycle. The primary goal of this treatment is to break down the polymer chains that hold the plastic together, allowing for the separation of its components and subsequent reuse. This method is particularly effective for plastics like polystyrene (PS) and polyvinyl chloride (PVC), which are commonly used in packaging and construction materials.
One common approach to chemical recycling is the use of solvents. Solvents with specific properties can be employed to dissolve the plastic, effectively breaking the polymer chains. For instance, polystyrene can be dissolved in chlorinated solvents like carbon tetrachloride or dichloromethane. The plastic is first ground into small pieces and then treated with the solvent, which dissolves the PS, leaving behind a solid residue. This residue can then be further processed or used as a feedstock for new products. However, it's important to note that the choice of solvent is critical, as some solvents may not effectively dissolve the plastic or may cause environmental concerns due to their toxicity.
Catalysts play a significant role in another chemical treatment process known as polymer chain scission. This technique involves using catalysts to initiate a chemical reaction that breaks the long polymer chains into smaller units. For example, in the recycling of polyvinyl chloride (PVC), metal catalysts like zinc or lead can be used to promote the chain scission reaction. The PVC is heated in the presence of these catalysts, which facilitate the breaking of the polymer chains, resulting in smaller vinyl chloride molecules. These molecules can then be further processed to create new PVC products or other materials.
The use of catalysts in chemical recycling offers several advantages. Firstly, it allows for the recycling of a wider range of plastics, including those that are difficult to recycle through mechanical methods. Secondly, catalysts can often operate under milder conditions, reducing energy consumption and minimizing the risk of material degradation. However, catalyst selection and optimization are crucial, as some catalysts may be expensive or require specific reaction conditions, making the process less economically viable.
In summary, chemical treatment, particularly through the use of solvents and catalysts, is a powerful technique for recycling thermosoftening plastics. It enables the breakdown of polymer chains, facilitating the separation of plastic components and their subsequent reuse. While solvents provide a direct approach to dissolving plastics, catalysts offer a more versatile method for chain scission, making chemical recycling a valuable tool in the sustainable management of plastic waste.
Who Buys Recycled Plastic? Uncovering the Demand for Sustainable Materials
You may want to see also
Re-melting and Molding: Melt recycled plastics and reshape them into new products
The process of recycling thermosoftening plastics, such as polystyrene (PS) and polycarbonate (PC), involves a method known as re-melting and molding, which is a crucial step in transforming used plastic materials into new products. This technique is particularly effective for these types of plastics due to their unique properties.
When thermosoftening plastics are recycled, the initial step is the collection and sorting of the used plastic items. These plastics are then cleaned to remove any contaminants, ensuring a higher quality of the final product. The cleaned plastic is then shredded or granulated into small pieces, making it easier to handle and process. This step is essential as it prepares the plastic for the re-melting process.
The next stage involves heating the shredded plastic to its melting point. Thermosoftening plastics have a relatively low melting temperature compared to other types of plastics, making this process more accessible. The plastic is melted and then poured into a mold, where it takes the shape of the desired product. This molding process can be done using various techniques, such as injection molding, blow molding, or compression molding, depending on the specific requirements of the product.
During the molding process, the plastic is cooled and solidified, forming the new product. This method allows for the creation of a wide range of items, including packaging materials, containers, and even electronic components. The beauty of this recycling technique lies in its ability to give new life to old plastics, reducing waste and promoting sustainability.
Re-melting and molding offer several advantages. Firstly, it allows for the creation of high-quality products with consistent properties, ensuring that the recycled plastic meets the required standards. Secondly, this process can be energy-efficient, as the melting temperature is generally lower than that of other recycling methods, reducing energy consumption. Additionally, the versatility of this technique enables the production of various plastic items, making it a valuable recycling approach for thermosoftening plastics.
Unraveling NYC's Juice Box Recycling Mystery: Paper or Plastic?
You may want to see also
Quality Control: Inspect recycled plastics for purity and consistency before reuse
Quality control is an essential step in the recycling process for thermosoftening plastics, ensuring that the recycled material meets the required standards and can be safely reused. This process involves a series of inspections and tests to evaluate the purity and consistency of the recycled plastic. Here's an overview of the quality control procedures:
Sorting and Classification: The first step in quality control is to sort and classify the recycled plastics. Different types of thermosoftening plastics, such as polypropylene (PP), polystyrene (PS), or polycarbonate (PC), require specific recycling methods. Advanced sorting techniques, including near-infrared (NIR) spectroscopy and optical sorting, are employed to separate plastics based on their type and color. This initial sorting ensures that only materials of the desired type are processed further.
Contaminant Removal: After sorting, the recycled plastics must be thoroughly cleaned to remove any contaminants. This process involves several stages. First, the plastics are shredded or granulated to increase the surface area, allowing for more effective cleaning. Next, they are washed using various cleaning agents and methods to eliminate dirt, labels, and other foreign matter. Advanced washing techniques, such as using high-pressure water jets or chemical treatments, can be employed to ensure a thorough clean.
Purity Testing: To assess the purity of the recycled plastic, several testing methods are utilized. One common technique is the use of Fourier-transform infrared spectroscopy (FTIR) to identify and quantify the different polymer types present. This non-destructive testing method provides detailed information about the plastic's composition. Additionally, particle size analysis can be performed to ensure that the recycled plastic meets the desired particle size distribution, which is crucial for its intended applications.
Consistency and Quality Assessment: Consistency in the quality of recycled plastics is maintained through rigorous inspection and testing. Visual inspections are conducted to identify any visible defects, such as discoloration, impurities, or damage. Automated inspection systems, utilizing machine vision technology, can enhance the accuracy and speed of this process. Furthermore, physical property testing, such as melt flow index (MFI) measurements, is performed to evaluate the plastic's flow characteristics, which are essential for processing and forming.
Reagent Testing and Certification: Before the recycled plastic is reused, it undergoes reagent testing to ensure its compatibility with various applications. This involves subjecting the material to specific chemical and physical tests to assess its performance and safety. Once the recycled plastic passes all the quality control tests, it is certified and ready for reuse in manufacturing processes, ensuring that it meets the required purity and consistency standards.
By implementing these quality control measures, the recycling process for thermosoftening plastics can produce a consistent and pure material, contributing to a more sustainable and efficient use of resources.
Unraveling the Mystery: Can Plastic Toothpicks Be Recycled?
You may want to see also
Frequently asked questions
Thermosoftening plastics, also known as thermoplastic resins, are a class of polymers that can be softened and hardened through heat and pressure. Unlike thermosetting plastics, which cure permanently and cannot be remolded, thermosoftening plastics can be remolded multiple times without losing their original properties. This characteristic makes them highly recyclable and suitable for various applications.
The recycling of thermosoftening plastics involves several steps. First, the used plastic items are collected, sorted, and cleaned to remove any contaminants. Then, the sorted plastics are shredded or granulated to reduce their size. Next, the plastic flakes or pellets are melted and then cooled to form new products. This process can be repeated multiple times without significant degradation in quality.
Yes, several recycling methods are employed for thermosoftening plastics. One common method is mechanical recycling, which involves physical processes like shredding, washing, and pelletizing to create new products. Another approach is chemical recycling, which uses various chemical processes to break down the plastic into its original monomers or building blocks, allowing for the creation of new materials. Advanced technologies like solvent-based recycling and gasification are also being explored to enhance the recycling efficiency.
Recycling thermosoftening plastics offers numerous advantages. It reduces the demand for virgin raw materials, conserving natural resources and energy. By reusing these plastics, we can minimize the amount of waste sent to landfills or incinerators, thus reducing environmental pollution. Additionally, recycling helps to decrease greenhouse gas emissions associated with the production of new plastics. It also promotes a circular economy, where materials are continuously reused and recycled, leading to a more sustainable and environmentally friendly approach to plastic waste management.