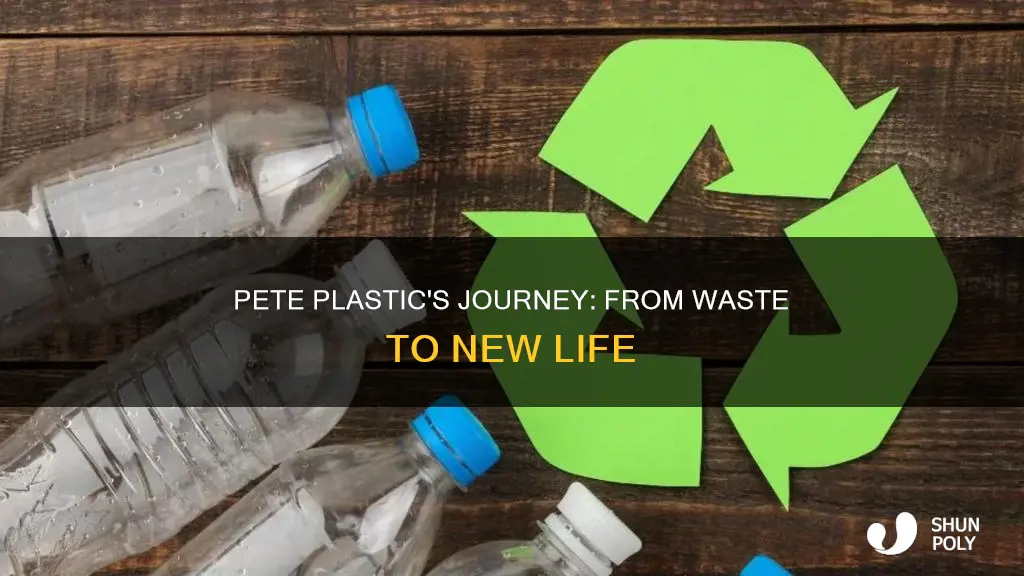
Pete plastic recycling is a crucial process in the journey towards a sustainable future. It involves transforming used plastic items, often those bearing the PET (polyethylene terephthalate) resin identification code, into new products. This recycling process begins with collecting and sorting the plastic waste, ensuring it is clean and free from contaminants. The sorted PET plastic is then shredded or granulated into small pieces, which are further processed to remove any remaining impurities. Through a process called polymerization, these plastic fragments are transformed into new raw materials, which can be used to create a wide range of products, from clothing and furniture to new bottles and containers. This innovative recycling method not only reduces the amount of plastic waste in landfills and oceans but also minimizes the demand for virgin plastic production, contributing to a more circular economy.
What You'll Learn
- Collection: Sorting and gathering PET plastic bottles from residential and commercial sources
- Cleaning: Removing contaminants like labels and caps to ensure purity for recycling
- Shredding: PET plastic is shredded into small flakes for easier processing
- Melting: Flakes are heated and melted to form a viscous liquid
- Molding: The molten plastic is shaped into new products like fibers or bottles
Collection: Sorting and gathering PET plastic bottles from residential and commercial sources
The process of recycling PET (polyethylene terephthalate) plastic bottles begins with the collection and sorting of these materials, which is a crucial step in ensuring the efficiency and effectiveness of the recycling process. PET bottles are widely used for packaging beverages, food, and various household products, making them a common household item. Therefore, a well-organized collection system is essential to gather these bottles from residential and commercial sources.
Collection efforts should focus on both residential and commercial areas to ensure a steady supply of PET bottles. In residential settings, this can be achieved through public awareness campaigns, recycling programs, or the implementation of color-coded recycling bins specifically for plastic bottles. Encouraging residents to separate their waste and place PET bottles in designated bins will facilitate the initial stage of recycling. Local governments or waste management companies can play a vital role in educating the public about the importance of recycling and providing the necessary infrastructure.
For commercial sources, such as restaurants, cafes, supermarkets, and offices, implementing recycling programs tailored to their needs is essential. Providing clearly labeled recycling bins and educating staff or employees about the proper disposal of PET bottles can significantly contribute to the collection process. Commercial establishments often generate substantial amounts of PET waste, and their cooperation is crucial for a successful recycling initiative.
During the collection phase, it is essential to maintain a high level of cleanliness to prevent contamination. PET bottles should be free from food residue, labels, and other debris. Contaminated bottles can compromise the recycling process and lead to downcycling or even waste. Therefore, proper cleaning and sorting techniques should be employed to ensure the quality of the collected materials.
Once collected, the PET bottles undergo a sorting process to separate them from other types of plastic and waste. This step is critical as it determines the quality and purity of the recycled material. Advanced sorting techniques, such as optical sorting and near-infrared (NIR) spectroscopy, can be utilized to identify and separate PET bottles from other plastics. These methods ensure that only PET bottles are processed further, maintaining the integrity of the recycling stream.
Recycling Confusion: Sorting Paper and Plastic, Demystified
You may want to see also
Cleaning: Removing contaminants like labels and caps to ensure purity for recycling
The process of recycling PET (polyethylene terephthalate) plastic, commonly used in beverage bottles, involves several crucial steps to ensure the material is clean and pure, ready for new product creation. One of the most important initial stages is cleaning, which involves removing various contaminants to meet the high standards required for recycling.
When PET bottles are collected for recycling, they often come with labels, caps, and sometimes even residual liquid or dirt. These items and substances need to be removed to prevent contamination and ensure the quality of the recycled material. The cleaning process typically begins with the removal of labels, which are often made of paper or a paper-like material coated with a thin layer of plastic. Labels can be tricky to separate from the PET bottle, as they are often glued or heat-sealed to the container. A common method is to use a sharp object, like a knife or a pair of scissors, to carefully cut the label away from the bottle, ensuring no residue or glue remains.
After label removal, the caps, usually made of a different type of plastic, need to be separated from the bottles. This step is essential because caps often have different recycling codes and may not be accepted by the same recycling streams as the bottles. Caps can be recycled separately, but they must be cleaned to remove any residual liquid or dirt. A simple way to clean caps is by soaking them in warm soapy water, which helps to loosen and remove any built-up grime. Rinsing the caps thoroughly with clean water ensures that no soap residue remains, making them suitable for recycling.
The cleaning process also involves removing any residual liquid or food particles from the PET bottles. This step is crucial to prevent cross-contamination and ensure the purity of the recycled material. PET bottles can be rinsed with clean water to remove any remaining liquid. For food particles, a more thorough cleaning may be required, which can be done by placing the bottles in a dishwasher or using a high-pressure water jet to ensure all contaminants are eliminated.
By following these cleaning procedures, the PET bottles are prepared for the next stage of recycling, where they will be shredded into small pieces called 'flakes'. These flakes are then cleaned further and processed into new products, such as polyester fibers for clothing or new beverage bottles, ensuring a continuous and sustainable cycle of material reuse. Proper cleaning techniques are vital to the success of PET recycling, contributing to a more efficient and environmentally friendly recycling process.
Unraveling the Mystery: Can Plastic Mailboxes Be Recycled?
You may want to see also
Shredding: PET plastic is shredded into small flakes for easier processing
The process of recycling PET (polyethylene terephthalate) plastic begins with the collection and sorting of PET-based materials, such as beverage bottles and food containers. Once sorted, the PET plastic is prepared for recycling through a process called shredding. This initial step is crucial as it transforms the large, bulky PET items into smaller, more manageable pieces, making the subsequent recycling process more efficient.
Shredding PET plastic involves feeding the material into a specialized machine designed for this purpose. These machines are often equipped with sharp blades or rotors that rotate at high speeds, effectively cutting the PET plastic into tiny fragments. The shredded PET is then separated into different sizes, with the smaller flakes being the primary focus. This size reduction is essential because it allows for better control over the recycling process and enables the creation of a more uniform product.
The shredded PET flakes are typically light in color and have a fluffy, granular appearance. These flakes are now ready for further processing. The next step in the recycling journey often involves cleaning and sorting the flakes to remove any contaminants, such as labels, caps, or other non-PET materials. This cleaning process ensures that the recycled PET meets the required quality standards for its intended use.
After cleaning, the PET flakes can be used in various ways. One common application is in the production of new PET bottles and containers. The flakes are melted and formed into pellets, which can then be molded or extruded into the desired shape. These pellets are a valuable raw material for manufacturers, allowing them to create new products while reducing the demand for virgin PET production.
Shredding is a critical step in the recycling chain for PET plastic, as it sets the foundation for the entire recycling process. By reducing the size of the PET material, this step enables more efficient sorting, cleaning, and processing, ultimately contributing to the successful transformation of used PET items into new, reusable products. It is a simple yet effective method that plays a vital role in the circular economy, promoting sustainability and reducing waste.
Unraveling the Mystery: Can Plastic Bowls Be Recycled?
You may want to see also
Melting: Flakes are heated and melted to form a viscous liquid
The process of recycling PET (polyethylene terephthalate) plastic, commonly used in beverage bottles, involves a crucial step called melting. This technique is employed to transform PET flakes, which are small pieces of PET plastic, into a usable material for various applications.
When PET flakes are subjected to high temperatures, they undergo a phase change and melt into a viscous liquid. This melting process is carefully controlled to ensure the PET remains in a molten state, allowing for easy manipulation and shaping. The temperature and duration of heating are critical factors in this stage, as they determine the quality and consistency of the final recycled product.
During melting, the PET flakes lose their solid structure and become a semi-liquid substance. This transformation is essential as it enables the subsequent steps of recycling, such as molding or extrusion, to create new products. The molten PET can be poured, shaped, or extruded into various forms, depending on the desired end-use.
One of the key advantages of melting PET flakes is the ability to recycle the material multiple times without significant degradation. This process allows for the creation of high-quality recycled PET, which can be used in the production of new bottles, textiles, and even furniture. By reusing PET in this manner, the recycling process becomes more sustainable and environmentally friendly.
In summary, the melting process is a vital step in recycling PET plastic. It involves heating PET flakes to a specific temperature, turning them into a viscous liquid, and preparing them for further processing. This technique showcases the potential of recycling to create valuable materials from waste, contributing to a more circular economy.
Eco-Friendly Blooms: Recycled Plastic's Role in Artificial Flowers
You may want to see also
Molding: The molten plastic is shaped into new products like fibers or bottles
The process of molding is a crucial step in recycling PET (polyethylene terephthalate) plastic, which is commonly used in beverage bottles and various other packaging materials. When PET plastic waste is collected and sorted, it is typically shredded or granulated to facilitate the recycling process. The shredded PET is then cleaned to remove any contaminants, such as labels, caps, or other non-PET materials. This cleaning step ensures that the recycled material meets the required standards for its intended use.
Once the PET is cleaned, it is transformed into a raw material called PET resin. This is done by heating the shredded PET in a process called pelletization. The resin is then cooled and formed into small pellets, which resemble tiny, solid plastic beads. These pellets are the building blocks for creating new products.
Molding is the art of shaping these PET resin pellets into various forms and products. It involves heating the molten PET resin to a temperature where it becomes pliable and can be easily molded. This molten state is achieved through the application of heat and pressure in specialized equipment called injection molding machines. These machines are designed to precisely control the temperature and pressure, ensuring the PET resin is in the ideal state for molding.
During the molding process, the molten PET is injected into a mold, which is a cavity or form that determines the shape of the final product. The mold is typically made of metal and is designed to create the desired shape, whether it's a bottle, a container, or a specific component for the automotive or electronics industries. As the PET resin is injected into the mold, it quickly cools and solidifies, taking the shape of the mold. This transformation from molten plastic to a solid, shaped product is the essence of molding.
After the PET product is formed, it can be used for various applications. For example, it can be made into fibers for clothing, carpets, or automotive interior components. It can also be molded into new bottles, containers, or even more complex structures like automotive parts or electronic enclosures. The versatility of PET in molding allows for a wide range of recycled products, contributing to a more sustainable and circular economy.
Unstain the Past: A Guide to Removing Stains from Recycled Plastic Shirts
You may want to see also
Frequently asked questions
Pete Plastic, a brand of plastic packaging, has a unique recycling process. It is designed to be recycled through a closed-loop system, ensuring that the material can be reused multiple times. The process begins with collecting the used Pete Plastic packaging, which is then sorted and processed to remove any contaminants. The plastic is then shredded and washed to clean it, followed by a process called "recycling granulation," where the plastic is melted and formed into small pellets. These pellets can be used to create new products, completing the recycling cycle.
Pete Plastic's recycling initiative has a significant positive impact on the environment. By implementing a closed-loop recycling system, they reduce the demand for virgin plastic production, which often relies on fossil fuels and contributes to environmental degradation. Recycling Pete Plastic helps conserve natural resources, lowers energy consumption, and minimizes the amount of waste sent to landfills or incinerators. This process also reduces greenhouse gas emissions, as recycling typically requires less energy compared to manufacturing new plastic from raw materials.
Yes, consumers play a crucial role in the successful recycling of Pete Plastic. Here are some guidelines:
- Always check for the recycling symbol on the packaging, typically a triangle with a number inside, to ensure it is made from the correct type of plastic.
- Rinse the packaging to remove any food residue or liquids, as contaminants can affect the recycling process.
- Flatten the packaging to save space and make it easier for recycling centers to process.
- Place the cleaned and prepared packaging in your local recycling bin, following the guidelines provided by your waste management authority.
- Encourage and support brands like Pete Plastic that prioritize sustainable practices and recycling initiatives.