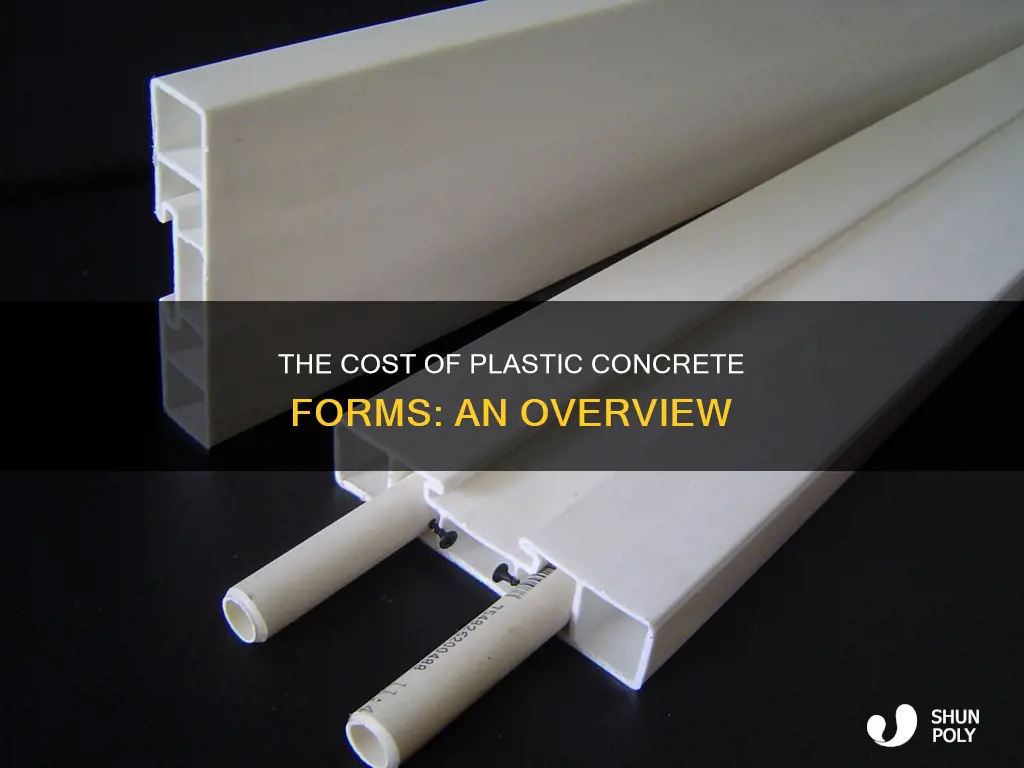
Plastic concrete forms are a durable and efficient alternative to wood or steel forms. They are flexible, long-lasting, and reusable, and can be used to create a variety of shapes and structures. Plastic forms are also more cost-effective than other options, as they require minimal finishing work and can be used hundreds of times. In this article, we will explore the benefits of plastic concrete forms in more detail and discuss how much they cost.
Characteristics | Values |
---|---|
Durability | Rigid plastic forms are durable, allowing them to withstand the pressure of wet concrete without bending or breaking. |
Reusability | Plastic concrete forms are reusable, unlike wood which can be used only 3-4 times before it becomes warped or twisted. |
Flexibility | Plastic is much easier to bend than lumber, giving users the option of tighter radiuses or long, sweeping curves. |
Smoothness | The smooth interior surface of plastic concrete forms produces concrete with a similar surface finish, reducing the need for extra finishing work. |
Insulation | A layer of foam insulation on some plastic forms helps keep the temperature of the poured concrete stable. |
Consistency | The inflexibility of these forms ensures consistent shape and thickness, improving the final product's quality. |
What You'll Learn
Plastic concrete forms are durable and efficient
Plastic concrete forms are a durable and efficient alternative to lumber. They are flexible, making them much easier to bend than wood, and giving users the option of tighter radiuses or long, sweeping curves. This flexibility is especially good for radius work. Plastic concrete forms can be free-formed to fit any curve up to a 3-foot bend radius. They are also long-lasting and reusable, with Plastiforms able to be used for hundreds of times over many years. In comparison, wood can be used only 3-4 times before it becomes warped or twisted.
Plastic concrete forms are also more durable than wood. They are rigid and able to withstand the pressure of wet concrete without bending or breaking. This results in stable, accurate pours and long-lasting concrete structures. The inflexibility of these forms ensures a consistent shape and thickness, improving the final product's quality.
The smooth interior surface of plastic concrete forms also produces concrete with a similar surface finish, reducing the need for extra finishing work, which saves time and money. The quality of the concrete is improved by the form's smooth surface, making it simpler to release and reducing defects.
Plastic concrete forms are also available in an insulated variety, which is popular in energy-efficient construction projects. They are made of polystyrene foam, which provides excellent insulation. They are also lightweight, easy to handle, and require minimal finishing work.
Ocean's Plastic Straw Problem: An Environmental Disaster
You may want to see also
They are reusable and long-lasting
Plastic concrete forms are a durable, long-lasting and reusable alternative to lumber. They are flexible, making them easier to bend than wood, and giving users the option of tighter radiuses or long, sweeping curves. They can be used hundreds of times for many years, compared to wood, which can be used only 3-4 times before it becomes warped or twisted.
Concrete forms are templates into which wet concrete is poured to shape it into required structures. Once the concrete has set, the forms are removed, leaving behind the concrete structure. Plastic forms are rigid, allowing them to withstand the pressure of wet concrete without bending or breaking. This results in stable, accurate pours and long-lasting concrete structures. The inflexibility of these forms ensures consistent shape and thickness, improving the final product's quality.
The smooth interior surface of plastic concrete forms produces concrete with a similar surface finish, reducing the need for extra finishing work, which saves time and money. The quality of the concrete is also improved by the form's smooth surface, making it simpler to release and reducing defects.
Traditional plastic concrete forms are non-degradable, robust, and reusable. They are made from materials such as copolymers, virgin resins, and UV stabilizers. They are used to pour walls in different projects, including residential, commercial, and agricultural projects. Insulated concrete forms are also reusable and made of polystyrene foam. They interlock like traditional concrete forms and are used to create insulated concrete walls. ICFs are popular in energy-efficient construction projects since they provide excellent insulation. They are lightweight, easy to handle, and require minimal finishing work.
The Ocean's Plastic Problem: Where Does It Come From?
You may want to see also
They are flexible and can be used for a variety of shapes
Plastic concrete forms are templates into which wet concrete is poured to shape it into required structures. Once the concrete has set, the forms are removed, leaving behind the concrete structure.
Plastic concrete forms are flexible and can be used for a variety of shapes. Plastiforms, for example, are long-lasting, reusable concrete form boards which are great for straight runs or a radius of any size. Each board is 3.5" tall to match typical 2x4 lumber and comes in 8' lengths. They can be free-formed to fit any curve up to a 3-foot bend radius.
Plastic's flexibility makes it much easier to bend than lumber, giving users the option of tighter radiuses or long, sweeping curves. This flexibility is also useful for radius work.
Rigid plastic forms for concrete are also durable, allowing them to withstand the pressure of wet concrete without bending or breaking. This results in stable, accurate pours and long-lasting concrete structures. The inflexibility of these forms ensures consistent shape and thickness, improving the final product's quality.
The Ocean's Plastic Crisis: An Ominous Warning
You may want to see also
They provide a smooth finish to the concrete
Plastic concrete forms are templates into which wet concrete is poured to shape it into required structures. Once the concrete has set, the forms are removed, leaving behind the concrete structure.
Plastic concrete forms are durable, allowing them to withstand the pressure of wet concrete without bending or breaking. This results in stable, accurate pours and long-lasting concrete structures. The inflexibility of these forms ensures consistent shape and thickness, improving the final product's quality.
The smooth interior surface of plastic concrete forms produces concrete with a similar surface finish. This reduces the need for extra finishing work, which saves time and money. The quality of the concrete is improved by the form's smooth surface, making it simpler to release and reducing defects.
Plastic concrete forms are classified into traditional and insulated concrete forms. Traditional plastic concrete forms are non-degradable, robust, and reusable. They are made from materials such as copolymers, virgin resins, and UV stabilizers. Insulated concrete forms are also reusable and made of polystyrene foam. They interlock like traditional concrete forms and are used to create insulated concrete walls. ICFs are popular in energy-efficient construction projects since they provide excellent insulation.
Plastic concrete forms are a durable alternative to lumber. Plastic’s flexibility makes it much easier to bend than lumber, giving users the option of tighter radiuses or long, sweeping curves. Plastiform is a type of plastic form board that is great for straight runs or a radius of any size. Each board is 3.5" tall to match typical 2x4 lumber and comes in 8' lengths.
Plastic in Our Bodies: What's the Harm?
You may want to see also
They are classified into traditional and insulated concrete forms
Concrete forms are templates into which wet concrete is poured to shape it into required structures. Once the concrete has set, the forms are removed, leaving behind the concrete structure. Plastic concrete forms are one of the types available in the market. They are classified into traditional and insulated concrete forms.
Traditional plastic concrete forms are non-degradable, robust, and reusable forms. They are made from materials such as copolymers, virgin resins, and UV stabilizers. They are used to pour walls in different projects, including residential, commercial, and agricultural projects.
Insulated concrete forms (ICFs) are also reusable and made of polystyrene foam. They interlock like traditional concrete forms and are used to create insulated concrete walls. ICFs are popular in energy-efficient construction projects since they provide excellent insulation. Additionally, they are lightweight, easy to handle, and require minimal finishing work.
Plastic concrete forms offer several advantages over other types of forms, such as wood and steel. Plastic is more flexible than wood, making it easier to bend and providing the option of tighter radiuses or long, sweeping curves. It is also more durable than wood, as plastiform can be used hundreds of times for many years, while wood can only be used 3-4 times before it becomes warped or twisted. Plastic forms are also more affordable than steel forms, which are typically reserved for larger industrial and commercial projects.
The durability and flexibility of plastic concrete forms make them a cost-effective and efficient choice for construction projects. Their smooth interior surface produces concrete with a similar finish, reducing the need for extra finishing work and saving time and money. The smooth surface also improves the quality of the concrete and makes it simpler to release, resulting in stable, accurate pours and long-lasting concrete structures.
The World's Plastic Problem: A Global Crisis
You may want to see also
Frequently asked questions
The cost of plastic concrete forms varies depending on the supplier and the quantity ordered. Alibaba, for example, has a minimum order of 200 pieces.
Plastic concrete forms are durable, flexible, and reusable. They are also more cost-effective than wood as they can be used hundreds of times, whereas wood can only be used 3-4 times before it becomes warped or twisted. Plastic is also easier to bend than lumber, allowing for tighter radiuses and long, sweeping curves.
There are two main types of plastic concrete forms: traditional plastic concrete forms and insulated concrete forms (ICFs). Traditional forms are made from materials such as copolymers, virgin resins, and UV stabilizers, while ICFs are made from polystyrene foam.
Plastic concrete forms can be purchased from suppliers such as Alibaba and Concrete Countertop Solutions.
Concrete forms are templates into which wet concrete is poured to shape it into the required structure. Once the concrete has set, the forms are removed, leaving behind the concrete structure.