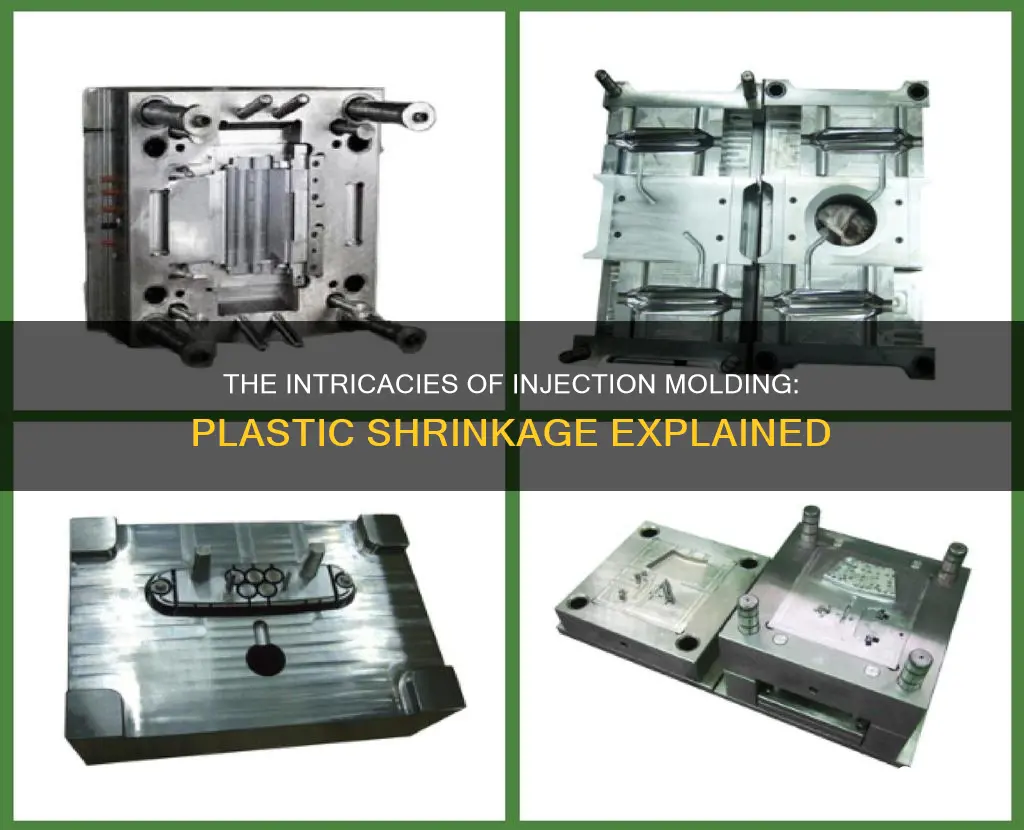
Plastic injection moulding is a manufacturing process that involves injecting plastic into a mould. During this process, the plastic can shrink by up to 25% as it cools and solidifies. This shrinkage is a normal part of the manufacturing process and is caused by the transition from the density of melted plastic to the density of its cooled, rigid state. The amount of shrinkage can vary depending on factors such as the type of material, wall thickness, and cooling rates. To avoid defects in the final product, it is important to compensate for shrinkage during the design stage and ensure that the part specifications meet the model.
Characteristics | Values |
---|---|
Typical shrink rate range | 0.001/in/in to 0.020/in/in |
Average shrink rate | 0.006/in/in |
Shrinkage range for 0.100 inch wall thickness | 0.005-0.007/in/in |
Shrinkage during the injection moulding process | Up to 25% |
What You'll Learn
Plastic shrinkage is caused by thermal contraction
When plastics are injected into a mould, they are subjected to a new set of conditions that affect how they shrink. Specifically, shear and extensional forces act on the polymer during the filling and packing phases. Volumetric shrinkage contracts the part in all dimensions and can result in warpage. This occurs when different areas of the part shrink unevenly, causing defects. For example, the "bowl" occurs when the perimeter has more volume, stays hotter, and shrinks more, causing the centre area to pop up. The "saddle" occurs when the perimeter freezes but the centre continues to shrink, pulling the perimeter in and causing it to buckle and/or twist to maintain its length.
To avoid warpage, it is critical to factor in the shrink rate at the tooling design stage, to ensure that the final parts meet the model specifications. The material supplier will usually provide a material data sheet that specifies a shrinking range for the material. For example, a material with a 0.100-inch wall thickness may have a shrinking range of 0.005-0.007/in/in, with an average shrink rate of 0.006/in/in.
After the part has been ejected, it may continue to shrink very slightly for several hours or even days until the temperature and moisture content stabilise to match that of the surrounding environment. To maintain consistency and suitable part stabilisation, the dimensional inspection should wait at least a day after part ejection.
Plastic Laminate Countertops: Installation Cost Guide
You may want to see also
The amount of shrinkage depends on the type of material
The primary cause of shrinkage is the transition from the density of melted plastic to the density of its cooled, rigid state. This process is affected by various factors, including the type of material, wall thickness, cooling rates, and moisture content. To maintain consistency and suitable part stabilization, it is recommended to wait at least a day after part ejection before performing a dimensional inspection, as minimal shrinkage can continue until the temperature and moisture content stabilize.
The Cost of Plastic Chairs: Exploring Price Factors
You may want to see also
Volumetric shrinkage results in warpage
Plastics can shrink up to 20-25% during the injection moulding process. This is known as volumetric shrinkage, which contracts the part in all dimensions. Volumetric shrinkage results in warpage, which is when the part shrinks unevenly and can cause severe defects. There are two well-known types of warpage: the "bowl" and the "saddle". The "bowl" occurs when the perimeter has more volume, stays hotter, and shrinks more, causing the centre area to pop up. The "saddle" occurs when the perimeter freezes but the centre continues to shrink, pulling the perimeter in and causing it to buckle and/or twist to maintain its length.
The amount of shrinkage depends on the type of material, wall thickness, cooling rates and other variables. The material supplier will usually provide a material data sheet that specifies a shrinking range for the material. For example, a 0.100-inch wall thickness might have a shrinking range of 0.005-0.007/in/in. The tooling engineer will scale the mould tooling by 1.00X to compensate for shrinkage so that the final part meets the model specifications.
To maintain consistency and suitable part stabilisation, the dimensional inspection should wait at least a day after part ejection. This is because the part may continue to shrink very slightly for several hours or even days until the temperature and moisture content stabilise to match that of the surrounding environment.
Acetone's Impact on Plastic Pipes: How Much to Melt?
You may want to see also
The majority of shrinkage occurs before the part is ejected from the mould
Plastic can shrink up to 25% during the injection moulding process. The amount of shrinkage depends on the type of material, wall thickness, cooling rates and other variables. The majority of shrinkage occurs before the part is ejected from the mould, but minimal shrinkage can continue after ejection as the moisture and temperature stabilise.
The primary cause of shrinkage is the transition from the density of melted plastic to the density of its cooled, rigid state. Volumetric shrinkage contracts the part in all dimensions and can result in warpage, which is when areas of the part shrink unevenly. This can cause severe part defects.
To avoid defects, it is critical to factor in the shrink rate at the tooling design stage, to ensure that the final parts meet the model specs. The tooling engineer simply scales the mould tooling by 1.00X to compensate for shrinkage. The material supplier will usually provide a material data sheet that specifies a shrinking range for the material.
The Cost of Producing Plastic Thermoses Explained
You may want to see also
Minimising the effects of shrinkage is essential for moulding parts accurately
Plastics can shrink up to 25% during the injection moulding process. The amount of shrinkage depends on the type of material, wall thickness, cooling rates and other variables. Minimising the effects of shrinkage is essential for moulding parts accurately.
The primary cause of shrinkage is the transition from the density of melted plastic to the density of its cooled, rigid state. As the plastic cools, it contracts, and this can result in warpage, where different areas of the part shrink unevenly, causing severe defects. To avoid this, it is critical to factor in the shrink rate at the tooling design stage. The material supplier will usually provide a data sheet that specifies a shrinking range for the material, which can be used to scale the mould tooling accordingly.
Additionally, to maintain consistency and suitable part stabilisation, it is recommended to wait at least a day after part ejection before performing a dimensional inspection. This allows the part to stabilise to match the temperature and moisture content of the surrounding environment, as minimal shrinkage can continue for several hours or even days after ejection.
By compensating for shrinkage and considering the stabilisation process, manufacturers can ensure that the final parts meet the desired specifications and minimise the effects of shrinkage on the accuracy of the moulded parts.
The High Cost of Removing Plastic from our Environment
You may want to see also
Frequently asked questions
Plastic can shrink up to 25% during the injection moulding process.
The amount of shrinkage depends on the type of material, wall thickness, cooling rates and moisture content.
The primary cause of shrinkage is the transition from the density of melted plastic to the density of its cooled, rigid state.
Warpage occurs when areas of the part shrink unevenly, causing severe part defects.
Shrinkage units are expressed as thousandths of an inch per linear inch (0.00X /in/in). The tooling engineer scales the mould tooling by 1.00X when calculating shrinkage.