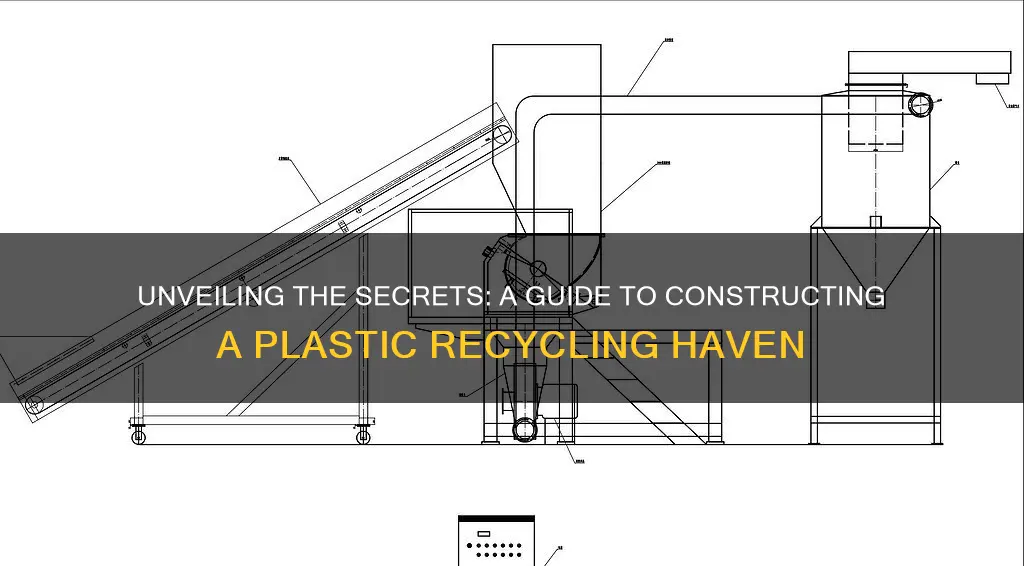
Building a plastic recycling plant is a complex process that requires careful planning and execution. It involves several key steps, from sourcing and sorting plastic waste to processing, cleaning, and transforming it into reusable materials. This guide will explore the essential components and considerations involved in establishing a successful plastic recycling facility, including the necessary equipment, processes, and environmental impact considerations.
What You'll Learn
- Feedstock: Source and prepare plastic waste for processing
- Sorting and Cleaning: Separate and clean plastics to ensure quality
- Milling and Shredding: Break down plastics into smaller, uniform pieces
- Melting and Molding: Transform plastic into usable forms
- Quality Control: Inspect and test recycled plastic products
Feedstock: Source and prepare plastic waste for processing
The first step in building a plastic recycling plant is to identify and secure a reliable source of feedstock, which is the raw material for your recycling process. Plastic waste is the primary feedstock for such plants, and its availability and quality are crucial for the success of the operation. You can source plastic waste from various places, including municipal waste streams, industrial sites, and specialized recycling centers.
When collecting plastic waste, it is essential to ensure a consistent and high-quality supply. This involves setting up efficient waste collection systems and partnerships with waste management companies or local authorities. The goal is to gather a diverse range of plastic types and colors, as different plastics have varying recycling processes and end-uses. Common plastics used in consumer products include PET (polyethylene terephthalate), HDPE (high-density polyethylene), PVC (polyvinyl chloride), LDPE (low-density polyethylene), and PP (polypropylene).
Once the waste is collected, it undergoes a preparation process to make it suitable for recycling. This includes sorting and cleaning the plastic materials to remove contaminants and non-plastic items. Manual sorting is often the first step, where workers separate different types of plastics based on their appearance and feel. This process can be aided by color-sorted bins and manual tools. After sorting, the plastics are cleaned to remove dirt, labels, and other debris. Cleaning methods may include washing with water and detergents, using air blowers to remove moisture, and sometimes even using specialized chemicals to break down certain contaminants.
Another critical aspect of feedstock preparation is shredding or granulating the sorted and cleaned plastics. This process reduces the size of the plastic waste, making it easier to handle and process. Shredding involves breaking down larger plastic items into smaller pieces, while granulating produces small, uniform plastic pellets. These pellets are then ready for further processing in the recycling plant, where they will be melted, molded, or used as feedstock for new products.
In summary, the feedstock stage is a critical phase in building a plastic recycling plant, requiring careful sourcing, efficient waste management systems, and thorough preparation techniques. By ensuring a steady supply of high-quality plastic waste, you lay the foundation for a successful recycling operation.
Unraveling the Mystery: Can No. 6 Plastic Be Recycled?
You may want to see also
Sorting and Cleaning: Separate and clean plastics to ensure quality
The initial step in establishing a plastic recycling plant is to focus on the crucial process of sorting and cleaning plastics to maintain high-quality standards. This process is essential as it directly impacts the efficiency and effectiveness of the entire recycling operation. Here's a detailed guide on how to approach this critical phase:
Sorting Plastics: Begin by setting up a comprehensive sorting system to separate different types of plastics. This is a critical step as each plastic type has unique properties and recycling methods. Start by creating a color-coded system or using advanced optical sorters that can identify different polymers based on their light reflection properties. For instance, PET (polyethylene terephthalate) and HDPE (high-density polyethylene) have distinct characteristics that can be detected by machines. Place these sorted areas in a sequence, starting with the most common and easily recyclable plastics like PET bottles, which are widely available and have a high recycling value. Then, move on to other types, ensuring a steady flow of sorted materials.
Manual Sorting and Quality Control: While automated sorting is efficient, manual inspection is equally important. Assign trained personnel to inspect the sorted plastics and remove any contaminants or low-quality materials. This step ensures that only the best-sorted plastics proceed to the cleaning stage. Educate your team on identifying common contaminants like food residue, labels, and non-plastic items. For instance, food-grade PET bottles should be free from any food particles or stains. Similarly, HDPE containers should be clean and free from any residue that might affect their recyclability.
Cleaning Process: Cleaning is a critical aspect of ensuring the quality of recycled plastics. Implement a multi-step cleaning process to remove impurities and prepare the plastics for further processing. Start with a pre-cleaning stage where you use water jets and brushes to remove large debris and surface contaminants. This step is crucial for removing any non-plastic items that might have been missed during sorting. Follow this with a more thorough cleaning process using industrial washing machines. These machines can effectively wash and rinse the plastics, removing any remaining contaminants. For example, use a combination of hot water and detergents to dissolve and remove any remaining food or label residue.
Drying and Inspection: After cleaning, ensure that the plastics are thoroughly dried to prevent moisture-related issues during the recycling process. Use industrial dryers or air blowers to remove excess water. Finally, conduct a final inspection to ensure that the cleaned plastics meet the required standards. This inspection should include checking for any remaining contaminants, verifying the integrity of the plastic, and ensuring it is free from damage.
By implementing a rigorous sorting and cleaning process, your plastic recycling plant will produce high-quality recycled materials, contributing to a more sustainable and efficient recycling system. This step is fundamental to the success of your plant and the overall environmental impact of your operations.
The Plastic Recycling Myth: Unveiling the Truth
You may want to see also
Milling and Shredding: Break down plastics into smaller, uniform pieces
The initial step in the plastic recycling process involves milling and shredding, a crucial phase that prepares the plastic waste for further processing. This stage aims to reduce the size of plastic materials, ensuring they are manageable and uniform, which is essential for efficient recycling. Here's a detailed breakdown of this process:
Milling: Milling is the initial mechanical process that begins with the reception of plastic waste. It involves feeding the plastic materials into a mill, a heavy-duty machine designed to break down large pieces of plastic into smaller fragments. The mill's rotating blades or rollers grind the plastic, reducing it to a consistent size. This process is highly effective in creating a uniform feedstock, ensuring that the subsequent stages of recycling can proceed smoothly. The output of the milling process is a fine, consistent-sized plastic powder or flakes, which are then ready for further processing.
Shredding: After milling, the plastic flakes or powders are fed into a shredder, another specialized machine designed for size reduction. Shredding is a more aggressive process compared to milling, as it involves cutting or tearing the plastic into even smaller pieces. The shredder's sharp blades or teeth create a uniform-sized plastic shred, which is crucial for the next steps in recycling. This process ensures that the plastic is broken down to a size suitable for washing, removing contaminants, and preparing it for the recycling stream. The shredded plastic can then be further processed to create new products or raw materials.
The milling and shredding process is a critical aspect of plastic recycling as it ensures that the plastic waste is transformed into a manageable and consistent form. This step requires specialized equipment and careful operation to achieve the desired size reduction. By breaking down plastics into smaller, uniform pieces, the recycling plant sets the foundation for efficient sorting, cleaning, and ultimately, the creation of new plastic products. This initial phase is a vital investment in the overall success and sustainability of the recycling process.
Unraveling the Mystery: Can Plastic Containers Be Recycled?
You may want to see also
Melting and Molding: Transform plastic into usable forms
The process of transforming recycled plastic into usable forms begins with the melting and molding stage, a crucial step in the recycling plant's operations. This phase requires specialized equipment and precise techniques to ensure the quality and consistency of the final products. Here's an overview of the melting and molding process:
Melting Process:
- Plastic Collection and Sorting: The first step is to collect and sort various types of plastic waste. Different plastics have unique melting points and properties, so proper sorting is essential. Common plastics include PET (polyethylene terephthalate), HDPE (high-density polyethylene), PVC (polyvinyl chloride), and LDPE (low-density polyethylene). Each type is then directed to its respective processing line.
- Shredding and Granulation: After sorting, the plastic waste is shredded into small pieces to facilitate uniform melting. These shredded pieces are then granulated, creating small, uniform pellets. This step ensures that the plastic is in a consistent and manageable form for the melting process.
- Melting Furnace: The granulated plastic is fed into a melting furnace, typically an industrial-grade machine designed to handle high temperatures. The furnace's temperature is carefully controlled to match the specific melting point of the plastic type. For example, PET melts at around 255°C (500°F), while HDPE melts at a slightly lower temperature. The plastic is melted to a viscous liquid state, ready for molding.
Molding Process:
- Mold Preparation: Molds are essential tools in the molding process, designed to give shape to the molten plastic. These molds can be of various sizes and shapes, depending on the intended product. They are made from metal or rubber and are carefully designed to ensure proper drainage and release of the molded part.
- Feeding the Melting Plastic: The molten plastic from the furnace is now ready to be shaped. It is carefully fed into the mold using specialized equipment, such as a plunger or a screw feeder. The temperature and pressure must be precisely controlled to ensure the plastic fills the mold evenly.
- Cooling and Solidification: Once the mold is filled, it is quickly cooled to solidify the plastic. This rapid cooling process is crucial to achieving the desired shape and strength. After cooling, the mold is opened, and the finished product is released.
- Quality Control: Each molded part undergoes rigorous quality control checks to ensure it meets the required specifications. This includes visual inspections, dimensional measurements, and sometimes, additional testing for strength and durability.
The melting and molding process is a delicate balance of temperature, pressure, and timing. It requires skilled operators and engineers to manage the equipment and ensure consistent quality. This stage transforms raw recycled plastic into a wide range of usable products, from packaging materials to automotive parts, contributing significantly to the circular economy.
Recycling Plastic: Energy Savings and Environmental Impact
You may want to see also
Quality Control: Inspect and test recycled plastic products
Quality control is a critical aspect of ensuring the reliability and safety of recycled plastic products. When building a plastic recycling plant, implementing rigorous inspection and testing procedures is essential to maintain high standards and meet consumer expectations. Here's an overview of the process:
Visual Inspection: Begin with a thorough visual examination of the recycled plastic materials. Inspect the feedstock for any visible contaminants such as dirt, debris, or foreign objects. Check for signs of damage, tears, or discoloration in the plastic flakes or pellets. This initial inspection helps identify obvious defects and ensures that only clean and suitable material proceeds to the next stages.
Material Testing: Conduct comprehensive testing to assess the quality and properties of the recycled plastic. Start with moisture content analysis to ensure the material is dry and free from excess water. Then, perform density measurements to determine the purity and consistency of the plastic. Use techniques like infrared spectroscopy to identify different types of plastics and ensure they are sorted correctly. Additionally, test for colorfastness and optical clarity to meet the desired product specifications.
Mechanical Testing: Evaluate the mechanical properties of the recycled plastic to ensure it can withstand the intended use. Conduct tensile tests to measure the material's strength and elasticity. Check for impact resistance by subjecting the plastic to controlled drops or impacts. These tests provide valuable insights into the material's durability and help identify any potential weaknesses or inconsistencies.
Dimensional Accuracy: Verify the dimensional accuracy of the recycled plastic products. Use precision measuring tools to check the dimensions against the specified requirements. Inspect for any deviations or inconsistencies in shape, size, and thickness. This step is crucial for maintaining product quality and ensuring that the recycled plastic meets the desired specifications.
Statistical Process Control (SPC): Implement SPC techniques to monitor and control the quality of the recycling process. Collect data on various parameters during the inspection and testing phases. Use control charts to identify any process variations or outliers. By analyzing this data, you can make informed decisions to optimize the recycling process and maintain consistent product quality.
Regularly reviewing and updating quality control procedures is essential to adapt to new challenges and technological advancements in the recycling industry. By combining visual inspection, material testing, mechanical assessments, and statistical analysis, a comprehensive quality control system can be established, ensuring that the recycled plastic products meet the required standards and consumer demands.
Wake County's LDPE 4 Plastic Recycling: Unlocking the Potential
You may want to see also
Frequently asked questions
A plastic recycling plant typically involves several essential components. These include a collection and sorting system to gather and categorize different types of plastic waste, a shredding or granulating machine to process the sorted plastics into smaller pieces or granules, a washing and drying unit to remove contaminants, and a pelletizing machine to create uniform plastic pellets. Additionally, you'll need a storage area for the recycled materials and an efficient transportation system to move the processed plastics.
Maintaining product quality is crucial in the recycling process. Start by implementing strict quality control measures during sorting to separate contaminants and ensure only clean and sorted plastics are processed. Use advanced screening techniques to identify and remove any foreign materials. Regularly maintain and calibrate your machinery to minimize defects. Implement a rigorous testing protocol for the recycled plastic pellets to ensure they meet industry standards and are free from impurities.
Establishing a plastic recycling facility offers significant environmental advantages. It helps reduce the amount of plastic waste that ends up in landfills or pollutes natural habitats. By recycling, you can conserve natural resources as it reduces the need for virgin plastic production, which often relies on fossil fuels. This process also lowers energy consumption compared to manufacturing new plastics, thus decreasing greenhouse gas emissions. Proper recycling can also minimize pollution from plastic waste, promoting a cleaner and healthier environment.
Running a plastic recycling plant may present several challenges. One of the main obstacles is the initial investment required for setting up the infrastructure and machinery. Securing funding and managing costs can be difficult. Another challenge is finding a consistent supply of high-quality plastic waste, as the availability and consistency of feedstock can vary. Additionally, maintaining a steady market for the recycled products and staying competitive in the recycling industry can be demanding.