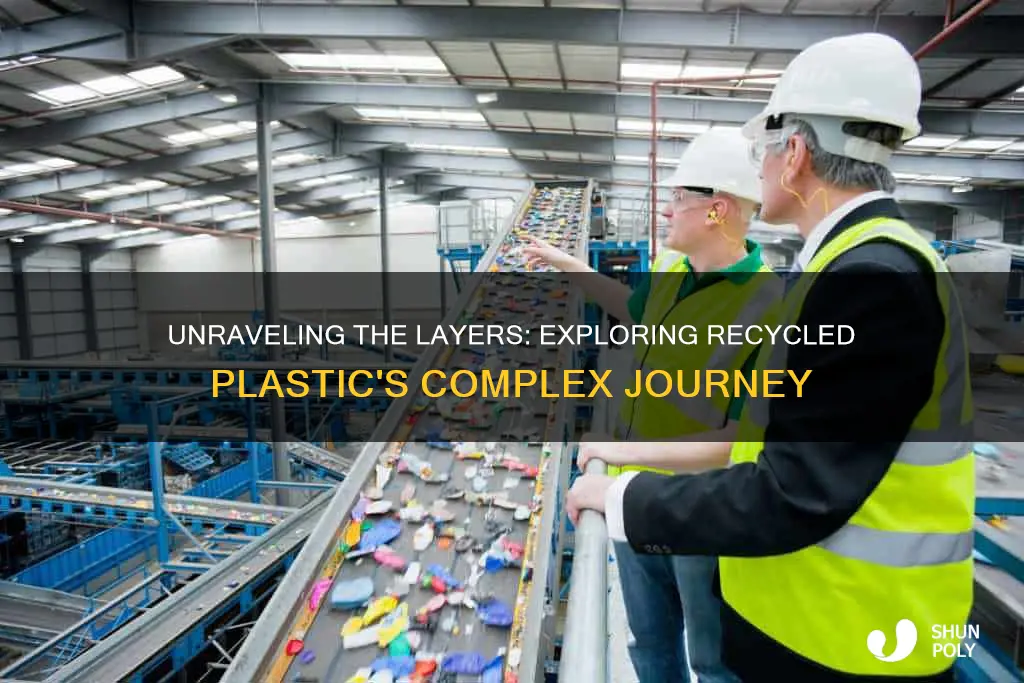
Recycling plastic is a complex process that involves multiple stages and levels of processing. The journey of recycled plastic typically begins with the collection and sorting of plastic waste, which is then sent to a recycling facility. At this stage, the plastic is sorted by type and color to ensure efficient processing. The sorted plastic is then cleaned and shredded into small pieces, a process known as shredding. These shredded pieces are further processed through various methods, such as washing, drying, and pelletizing, to create a usable material. The final product can be in the form of pellets, flakes, or even granulated plastic, which can then be used to manufacture new products. Understanding the different levels of recycling is crucial to comprehending the entire process and the quality of the recycled material.
What You'll Learn
Collection: Plastic waste is gathered from various sources
Plastic waste collection is a critical step in the recycling process, and it involves a systematic approach to gather plastic materials from various sources. This initial phase sets the foundation for effective recycling, ensuring that the collected plastics are suitable for processing and recycling. The collection process is a complex operation that requires careful planning and coordination to ensure the right types of plastics are obtained.
The sources of plastic waste are diverse and include residential areas, commercial establishments, industrial sites, and public spaces. In residential areas, waste collection often involves door-to-door recycling programs or designated drop-off points where citizens can deposit their plastic waste. These programs encourage community participation and help educate residents about proper waste segregation. Commercial establishments, such as shops, restaurants, and offices, generate significant amounts of plastic waste. Implementing recycling bins in these locations and providing clear guidelines on acceptable plastic types can significantly improve waste management.
Industrial sites, including manufacturing plants and warehouses, produce substantial plastic waste. These facilities often have dedicated recycling systems in place, such as on-site collection bins or partnerships with waste management companies. Proper waste segregation at the source is crucial in these settings to ensure that plastics are sorted according to their types and purity. Public spaces, such as parks, beaches, and streets, also contribute to plastic waste. Community clean-up initiatives and public awareness campaigns can engage citizens in collecting and sorting plastic waste from these areas.
The collection process should be designed to handle different types of plastics, as not all plastics are recyclable. Common plastic types include PET (polyethylene terephthalate), HDPE (high-density polyethylene), PVC (polyvinyl chloride), LDPE (low-density polyethylene), and PP (polypropylene). Each type has specific recycling requirements, and proper identification is essential. For instance, PET bottles are widely accepted in recycling programs, while PVC may have limited recycling options due to its chemical composition.
Efficient collection methods include implementing color-coded bins or bags for different plastic types, providing clear instructions on waste segregation, and offering incentives for participation. Waste management companies play a vital role in this process, ensuring that collected plastics are transported safely and securely to recycling facilities. They may also provide education and support to communities and businesses to improve recycling rates.
3D-Printed Homes: The Future of Sustainable Housing?
You may want to see also
Sorting: Materials are separated by type and color
The process of recycling plastic involves a crucial step known as sorting, which is essential for efficient and effective recycling. This step ensures that different types of plastic materials are separated, allowing for proper recycling and reducing contamination. The primary goal is to organize plastics by their type and color, a practice that significantly impacts the quality of the recycled material.
When sorting plastics, the first step is to identify the various types of plastic resins. These resins are typically indicated by a number inside a triangle on the bottom of the plastic item, known as the resin identification code. Common types include PET (polyethylene terephthalate), HDPE (high-density polyethylene), PVC (polyvinyl chloride), LDPE (low-density polyethylene), and PP (polypropylene). Each type has unique properties and applications, and separating them is vital for maintaining the integrity of the recycling process. For instance, PET is widely used for beverage bottles and should not be mixed with other types, as it has a different melting point and can contaminate other plastics.
Color separation is another critical aspect of this process. Plastic items can vary in color, and sorting by color ensures that similar materials are grouped together. This practice is particularly important for clear and colored plastics, as they can be recycled separately to maintain the desired color in the recycled product. For example, clear PET bottles can be recycled to produce new clear containers, while colored PET bottles might be used for different applications, such as fiber production.
The sorting process often involves manual labor, where workers carefully examine each item and separate it according to type and color. This meticulous work is essential, especially in large-scale recycling facilities, to ensure that the materials are correctly categorized. Advanced technologies, such as optical sorters, can also be employed to identify and separate plastics based on their color and type, further streamlining the process.
By implementing a comprehensive sorting system, recycling centers can improve the overall efficiency of plastic recycling. This step is fundamental to producing high-quality recycled plastic products and reducing the environmental impact of plastic waste. It also plays a crucial role in meeting the demands of various industries that rely on recycled materials, contributing to a more sustainable and circular economy.
America's Recycling Reality: Do Plastic Centers Deliver?
You may want to see also
Cleaning: Items are washed and prepared for processing
The process of recycling plastic involves several stages, and the first crucial step is cleaning. This initial cleaning process is essential to ensure the quality and efficiency of the recycling procedure. When items made of plastic are collected for recycling, they often contain various contaminants, which can hinder the recycling process and potentially damage machinery. Therefore, a thorough cleaning process is imperative.
Items destined for recycling are first sorted based on their type and color. This initial sorting helps in categorizing plastics into different streams, such as PET (polyethylene terephthalate), HDPE (high-density polyethylene), and LDPE (low-density polyethylene). Each type of plastic has its own unique properties and applications, and proper sorting ensures that they are recycled accordingly. After sorting, the items are washed to remove any remaining dirt, labels, and non-plastic components. This washing process typically involves the use of water and sometimes specialized cleaning agents to ensure a thorough clean.
The cleaning process is designed to eliminate any debris, labels, and contaminants that may be present on the plastic items. This includes removing labels, which are often made of a different type of plastic and can interfere with the recycling of the main plastic component. The washing process may involve multiple stages, starting with a pre-wash to remove loose dirt and then a more thorough wash to ensure the removal of any stubborn contaminants. High-pressure water jets and specialized cleaning solutions are commonly used to ensure a comprehensive clean.
Once the items are washed, they are inspected to ensure that they meet the required standards for recycling. This inspection helps identify any remaining contaminants or damage that may have occurred during the cleaning process. Any items that do not pass the inspection are often set aside for alternative disposal methods, ensuring that only clean and suitable plastic materials proceed to the next stage of recycling.
After cleaning, the processed plastic items are ready for further treatment and recycling. This initial cleaning step is a critical phase in the recycling process, as it sets the foundation for the quality and efficiency of the entire recycling journey. Proper cleaning ensures that the recycled plastic can be utilized to create new products, contributing to a more sustainable and circular economy.
Plastic Recycling Codes: Unlocking Water Safety Secrets
You may want to see also
Shredding/Grinding: Plastic is broken down into small pieces
The process of recycling plastic involves several stages, each crucial for transforming waste plastic into reusable materials. One of the initial steps in this journey is shredding or grinding plastic waste. This process is a fundamental part of plastic recycling, as it reduces the size of plastic items, making them easier to handle and process further.
When plastic waste is collected, it is often sorted to separate different types of plastics, ensuring that the recycling process is efficient and effective. After sorting, the plastic is then shredded or ground. This step is particularly important for larger plastic items like bottles, containers, and even car parts, which need to be broken down into smaller pieces. The shredding or grinding process can be done using various machines, such as shredders, grinders, or even specialized plastic recycling equipment. These machines are designed to cut, tear, or grind the plastic into tiny fragments or flakes.
The goal of this shredding/grinding process is to create a uniform size of plastic particles, often referred to as 'flakes' or 'granules'. This uniformity is essential for the subsequent stages of recycling. Smaller pieces increase the surface area of the plastic, allowing for better mixing and processing with other materials. The shredded or ground plastic can then be further processed through washing to remove any contaminants, followed by drying and pelletizing to create a final product ready for manufacturing new items.
This initial step of shredding/grinding is a critical phase in the recycling chain, as it sets the foundation for the entire recycling process. It ensures that the plastic waste is prepared in a way that maximizes its potential for reuse, contributing to a more sustainable approach to managing plastic materials. By breaking down plastic into small, manageable pieces, we lay the groundwork for the creation of new products, reducing the demand for virgin plastic production and minimizing environmental impact.
Transforming Plastic Waste: The Art of Recycling for a Greener Future
You may want to see also
Melting/Reforming: Molten plastic is reshaped into new products
The process of recycling plastic involves several stages, and one crucial step is melting or reforming the plastic to create new products. This method is particularly useful for transforming post-consumer plastic waste into valuable materials. When plastic is collected, sorted, and prepared, it is often in the form of flakes or small pellets. These plastic fragments are then fed into a specialized machine designed for melting.
The melting process begins with the plastic flakes being heated to extremely high temperatures, typically around 200-300 degrees Celsius, depending on the type of plastic. This heat is applied uniformly to ensure that the plastic melts completely without burning or degrading. As the plastic reaches its melting point, it transitions from a solid state to a liquid state, becoming a molten mass. The molten plastic is then carefully handled and processed to ensure the desired outcome.
One common technique used in this stage is extrusion. The molten plastic is forced through a die or a mold, which gives it the desired shape. This process is often used to create new products such as plastic pellets, fibers, or even custom-shaped items. For example, in the textile industry, molten plastic can be extruded to form plastic fibers, which are then used to create fabrics or textiles for various applications.
Another approach is injection molding, where the molten plastic is injected into a mold to create complex shapes. This method is widely used in manufacturing industries to produce a wide range of plastic products, from automotive parts to consumer electronics. The mold is designed with specific cavities or shapes, and the molten plastic is carefully injected and cooled to set the desired form.
After the molten plastic is reshaped, it can be further processed to enhance its properties or create new materials. For instance, the reformed plastic can be blended with other materials to improve strength, flexibility, or durability. This blending process allows for the creation of composite materials, which find applications in construction, automotive, and electronics industries. The versatility of this recycling method ensures that plastic waste can be transformed into valuable resources, reducing the demand for virgin plastic production and minimizing environmental impact.
Apple Sauce, Plastic Dilemma: Recycling or Not?
You may want to see also
Frequently asked questions
The recycling process for plastic typically involves several stages, but the exact number can vary depending on the type of plastic and the recycling method. Generally, it includes collection, sorting, cleaning, processing, and manufacturing.
No, not all plastics are recyclable. The recycling symbol on plastic items, often called the resin identification code, indicates the type of plastic. Common recyclable plastics include PET (polyethylene terephthalate) and HDPE (high-density polyethylene), but others like PVC and polystyrene may have limited recycling options.
After collection, plastic waste is sorted based on its type and color. It then undergoes cleaning to remove contaminants like labels, dirt, and non-plastic materials. The cleaned plastic is processed into small flakes or pellets, which can be used to manufacture new products.
Yes, the recycling process can be categorized into different levels or stages. These levels include primary recycling, where the original plastic material is reprocessed, and secondary recycling, which involves downcycling, where the plastic is transformed into a different product of lower quality.
The number of recycling levels can affect the environmental impact and quality of the recycled material. Each recycling process may result in energy loss and degradation of the plastic's properties. Multiple recycling levels can lead to a decrease in the quality and value of the recycled product, making it less sustainable in the long term.