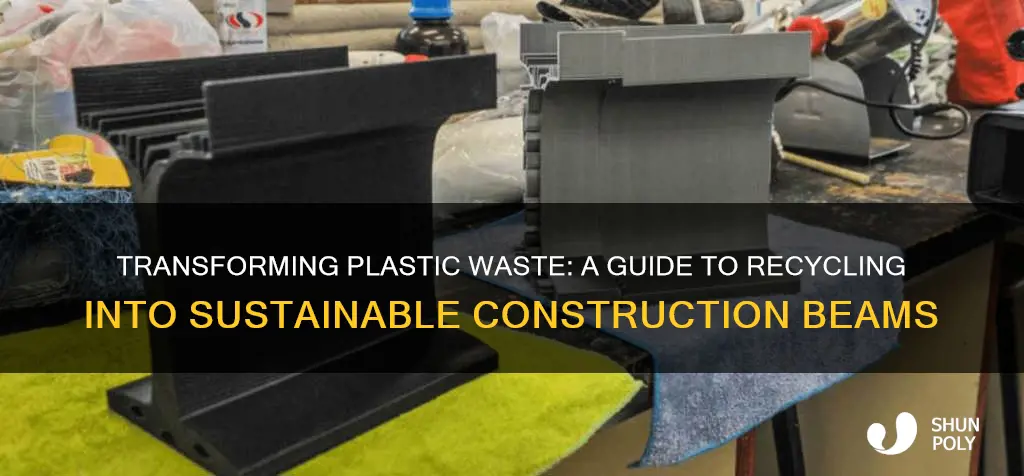
Recycling plastic into construction beams is an innovative approach to sustainable building practices. This process involves transforming plastic waste into a valuable resource, creating a more circular economy. By utilizing plastic recycling technology, construction beams can be produced, offering a lightweight yet sturdy alternative to traditional materials. This method not only reduces the environmental impact of plastic waste but also provides a unique and eco-friendly solution for the construction industry, contributing to a greener and more resilient future.
What You'll Learn
- Plastic Collection: Gather and sort plastic waste for construction beam production
- Melt and Mold: Heat and shape plastic into structural beams
- Reinforcement Techniques: Use steel or glass fibers to strengthen plastic beams
- Testing and Quality Control: Ensure structural integrity through rigorous testing
- Construction Application: Integrate recycled plastic beams into building frameworks
Plastic Collection: Gather and sort plastic waste for construction beam production
The process of recycling plastic into construction beams begins with a crucial step: plastic collection. This initial phase is fundamental to the entire recycling journey, ensuring that the right materials are gathered and prepared for transformation. Here's a detailed guide on how to effectively collect and sort plastic waste for construction beam production:
Collection Methods:
- Public Awareness and Drop-off Points: Educate the community about the importance of recycling plastic. Set up designated drop-off points or collection centers where people can conveniently bring their plastic waste. This could be in the form of public bins, collection trucks, or even mobile apps that provide information on the nearest collection site.
- Partnership with Businesses: Collaborate with local businesses, especially those that generate significant plastic waste, such as grocery stores, restaurants, and manufacturing plants. Arrange for regular collections of their plastic waste, ensuring a steady supply of raw materials for your recycling project.
- Household Collection: Encourage households to separate their plastic waste, especially those with easy-to-recycle items like water bottles, food containers, and packaging. Provide clear guidelines on what types of plastic are accepted to ensure the collection process is efficient.
Sorting and Classification:
Once the plastic waste is collected, efficient sorting is essential to separate it into different types and qualities. This step ensures that the recycled plastic beams will meet the required standards.
- Manual Sorting: Employ trained personnel to manually sort the plastic waste. This process involves identifying and separating different types of plastics based on their resin identification codes (e.g., PET, HDPE, PVC). Manual sorting is particularly useful for small-scale operations or when dealing with a variety of plastic types.
- Automated Sorting Systems: For larger-scale operations, consider investing in automated sorting systems. These machines use techniques like air classification, gravity separation, and optical sorting to separate plastics based on their density, shape, and color. Automated sorting increases efficiency and reduces the risk of human error.
- Quality Control: Implement a quality control process to assess the sorted plastic waste. This may include visual inspections, density testing, and moisture content measurements. Removing contaminated or low-quality plastic ensures that the final construction beams are durable and safe.
By focusing on effective plastic collection and meticulous sorting, you lay the foundation for successful plastic recycling into construction beams. This process not only reduces environmental waste but also contributes to sustainable building practices, showcasing the potential of recycled materials in the construction industry.
Unraveling the Mystery: Can Plastic Chocolate Boxes Be Recycled?
You may want to see also
Melt and Mold: Heat and shape plastic into structural beams
The process of transforming plastic waste into structural beams involves a methodical approach to melting and molding the material. This technique not only recycles plastic but also creates a sustainable and durable building material. Here's a step-by-step guide to achieving this:
Melting and Molding Process:
- Collection and Sorting: Begin by collecting various types of plastic waste, ensuring they are sorted by type to facilitate the recycling process. Common construction plastics like polypropylene (PP), high-density polyethylene (HDPE), and polyvinyl chloride (PVC) are ideal for this application.
- Shredding and Grinding: The sorted plastic is then shredded into small pieces and ground into a fine powder. This step ensures that the plastic is reduced to a manageable size, making it easier to process further.
- Melting: The ground plastic is fed into a specialized melting machine, typically a plastic extruder. The machine heats the plastic to its melting point, which varies depending on the type of plastic. For example, PP melts at around 160-170°C, while HDPE requires a slightly higher temperature of 130-150°C. This step requires precise temperature control to ensure the plastic is fully molten but not burned.
- Extrusion: Once melted, the plastic is extruded through a die to create a continuous strand or profile. The die's design will determine the shape of the final beam. For structural beams, a rectangular or square cross-section is common, with dimensions tailored to the specific project requirements.
- Cooling and Hardening: After extrusion, the plastic strand is cooled rapidly using water or air. This cooling process solidifies the plastic, giving it structural integrity. The cooling rate is critical to achieving the desired beam properties.
- Molding and Shaping: The cooled plastic strand is then fed into a molding machine, where it is shaped into the desired beam form. This step involves applying pressure and heat to the plastic, forcing it into a mold cavity. The mold's design will dictate the final beam's appearance and structural characteristics. Advanced molding techniques, such as compression molding, can be employed to ensure consistent quality.
- Post-Processing: After molding, the beams may undergo additional processes like trimming excess material, edge finishing, and surface treatment to enhance their appearance and performance.
This melt-and-mold process allows for the creation of custom-shaped structural beams, offering a sustainable alternative to traditional construction materials. By recycling plastic waste, this method contributes to a circular economy, reducing the environmental impact of the construction industry.
Reusing Plastic Cups: A Guide to Eco-Friendly Recycling and Upcycling
You may want to see also
Reinforcement Techniques: Use steel or glass fibers to strengthen plastic beams
The use of reinforcement techniques, such as incorporating steel or glass fibers, is a crucial aspect of enhancing the structural integrity and performance of plastic beams in construction. These fibers provide the necessary strength and stiffness to the plastic material, making it suitable for load-bearing applications. Here's an overview of the process and benefits:
Reinforcement with Steel Fibers:
Steel fibers are an excellent choice for reinforcing plastic beams due to their high strength-to-weight ratio. When mixed with plastic, these fibers create a composite material with improved mechanical properties. The process involves dispersing the steel fibers evenly throughout the plastic matrix during the manufacturing stage. This can be achieved through various methods, such as extrusion or pultrusion, where the plastic and fibers are combined and shaped into the desired beam form. The steel fibers act as a network, providing enhanced tensile strength and reducing the likelihood of plastic deformation under stress. This technique is particularly useful for heavy-duty construction applications, ensuring the beams can withstand significant loads and environmental stresses.
Reinforcement with Glass Fibers:
Glass fibers offer a lightweight and cost-effective alternative to steel fibers for plastic beam reinforcement. They provide excellent resistance to corrosion and chemical degradation, making them ideal for a wide range of construction environments. Similar to steel fiber reinforcement, glass fibers are dispersed within the plastic matrix during the manufacturing process. This technique allows for the creation of a composite material with superior strength and durability. Glass fiber-reinforced plastic beams exhibit improved impact resistance and can handle dynamic loads effectively. This method is especially valuable for applications where weight reduction is essential, such as in the construction of lightweight structures or bridges.
Both steel and glass fiber reinforcements offer distinct advantages, and the choice depends on the specific project requirements. Steel fibers provide exceptional strength and are commonly used in high-performance applications, while glass fibers offer a balance of strength and cost-effectiveness. The incorporation of these fibers into plastic beams ensures a more robust and reliable construction material, contributing to the overall safety and longevity of building structures. This reinforcement technique is a key factor in the successful recycling and utilization of plastic in the construction industry.
Transforming Car Plastic: The Recycling Process Unveiled
You may want to see also
Testing and Quality Control: Ensure structural integrity through rigorous testing
The process of recycling plastic into construction beams involves transforming plastic waste into a usable material that can be utilized in building structures. However, to ensure the structural integrity and safety of these beams, rigorous testing and quality control measures are essential. This process begins with the selection of suitable plastic types, as not all plastics are ideal for construction applications. High-density polyethylene (HDPE) and polypropylene (PP) are commonly chosen due to their strength and durability. The plastic waste is then cleaned, sorted, and shredded to create a consistent feedstock for the manufacturing process.
One critical aspect of testing is the evaluation of the mechanical properties of the recycled plastic beams. These properties include tensile strength, compressive strength, and impact resistance. Tensile testing involves applying force to the beam until it fails, providing data on its ability to withstand pulling forces. Compressive testing assesses the beam's ability to support loads by applying pressure from above. Impact resistance testing simulates real-world conditions by dropping or subjecting the beams to controlled impacts to ensure they can absorb and distribute energy effectively.
Non-destructive testing methods are also employed to assess the internal structure of the beams without causing damage. Techniques such as ultrasonic testing and radiographic testing can identify any voids, imperfections, or internal defects within the plastic material. These methods ensure that the recycled plastic beams meet the required standards and are free from potential weaknesses that could compromise their structural integrity.
Additionally, environmental testing is crucial to determine the long-term performance of the beams in various conditions. This includes exposure to different temperatures, humidity levels, and UV radiation. By simulating real-world environmental factors, engineers can assess the beam's resistance to weathering, corrosion, and degradation over time. This testing ensures that the recycled construction beams can withstand the challenges posed by different climates and outdoor conditions.
Quality control also involves visual inspections and dimensional measurements. Skilled technicians examine the beams for any visible defects, such as cracks, voids, or discolored areas, which may indicate processing issues or contamination. Precise measurements are taken to verify that the beams meet the specified dimensions and tolerances, ensuring they can be seamlessly integrated into construction projects.
In summary, rigorous testing and quality control are vital to guarantee the structural integrity and safety of recycled plastic construction beams. By employing a combination of mechanical, non-destructive, and environmental testing, along with visual inspections, engineers can ensure that the recycled material meets or exceeds the required standards. This comprehensive approach provides confidence in the performance and reliability of recycled plastic beams, making them a viable and sustainable alternative in the construction industry.
Laundry Jug Recycling: Uncovering the Truth
You may want to see also
Construction Application: Integrate recycled plastic beams into building frameworks
The integration of recycled plastic beams into building frameworks presents a sustainable and innovative approach to construction. This method not only reduces waste but also offers a lightweight, durable alternative to traditional building materials. Here's a detailed guide on how to implement this construction application:
Design and Planning: Begin by designing the building structure with recycled plastic beams in mind. Architects and engineers can create detailed blueprints, ensuring that the dimensions and specifications of the beams align with the overall construction plan. Consider the load-bearing requirements and choose the appropriate thickness and width of the plastic beams to support the building's weight.
Material Sourcing: Source recycled plastic materials from local recycling centers or waste management facilities. High-density polyethylene (HDPE) and polypropylene (PP) are commonly used plastics for this purpose due to their strength and durability. Collect and process the plastic waste to ensure it meets the quality standards required for construction. This may involve sorting, cleaning, and potentially shredding or grinding the plastic to create a uniform material.
Beam Manufacturing: Fabricate the recycled plastic beams using various manufacturing techniques. One common method is extrusion, where the processed plastic is melted and forced through a die to create a continuous beam. This process allows for precise control over the beam's dimensions and can produce beams in various shapes and sizes. Alternatively, molding or injection molding can be employed to create custom-shaped beams, offering flexibility in design.
Construction Implementation: During the construction phase, integrate the recycled plastic beams into the building framework. Start by laying a foundation and securing the beams to the ground using appropriate fasteners. Ensure that the beams are properly aligned and spaced according to the design specifications. Connect the beams to form a sturdy framework, providing structural integrity to the building. The lightweight nature of plastic beams can simplify the construction process, making it faster and more efficient.
Benefits and Considerations: Recycled plastic beams offer several advantages, including reduced weight, improved insulation properties, and enhanced fire resistance compared to some traditional materials. However, it is essential to consider the specific requirements of the building project. Factors such as local building codes, climate conditions, and the overall structural design should influence the choice of materials. Regular maintenance and inspections can ensure the longevity and safety of the building.
Plastic Hangers: Can They Be Recycled in Ontario?
You may want to see also
Frequently asked questions
Typically, high-density polyethylene (HDPE) and polypropylene (PP) are the most commonly used plastics for this purpose. These materials are durable, lightweight, and have good structural properties, making them ideal for creating strong and stable beams.
The process begins with collecting and sorting plastic waste, ensuring it is clean and free from contaminants. The sorted plastic is then shredded or granulated to reduce its size. Next, the plastic is heated and extruded into a continuous sheet or profile, which is then cut or shaped into the desired beam dimensions. Finally, the beams are cooled and cured to achieve their final form.
Recycled plastic beams offer several benefits. They are lightweight, reducing transportation and handling costs. Plastic beams are also resistant to corrosion, rot, and insect damage, making them a durable alternative to traditional wood or metal beams. Additionally, the use of recycled materials contributes to sustainability and reduces the demand for virgin resources.
Absolutely! Recycled plastic beams have proven to be effective in load-bearing structures. They can support significant weights and provide structural integrity when properly designed and installed. However, it is essential to consider factors like environmental conditions, expected loads, and local building codes to ensure the beams meet the required standards.
One challenge is the potential for plastic degradation over time due to environmental factors like UV radiation and temperature fluctuations. To mitigate this, manufacturers often add stabilizers and UV inhibitors to the plastic during the recycling process. Another consideration is the initial cost, as recycled plastic beams might be more expensive than traditional materials, but their long-term benefits and sustainability make them a valuable investment.