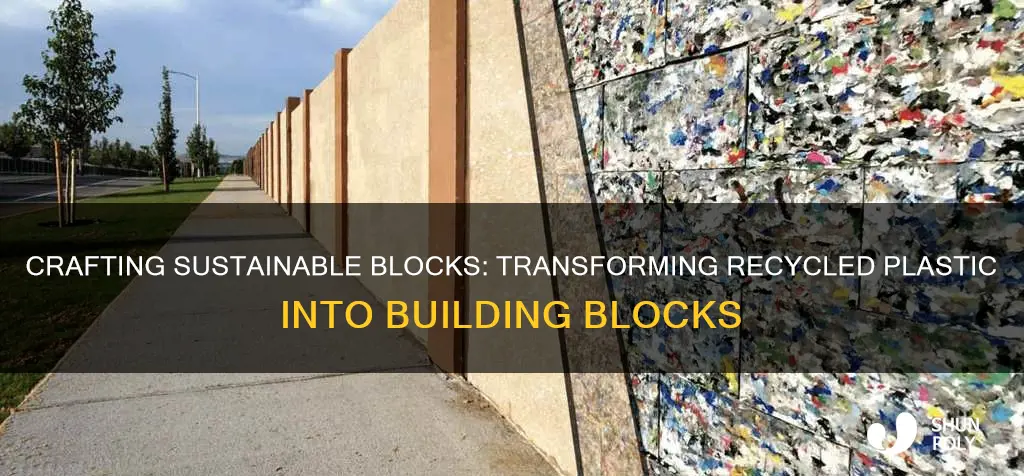
Creating blocks from recycled plastic is an innovative and sustainable way to reduce waste and build eco-friendly structures. This process involves collecting and sorting plastic waste, which is then cleaned and shredded into small pieces. These plastic pieces are melted and poured into molds to create solid blocks. The blocks can be used for various purposes, such as construction, landscaping, or even as a raw material for other products. This method not only helps in waste management but also promotes a circular economy, where resources are reused and recycled, reducing the demand for new materials and minimizing environmental impact.
What You'll Learn
Collection: Gather clean, sorted plastic waste from various sources
The first step in creating blocks from recycled plastic is to ensure you have a steady supply of clean and sorted plastic waste. This process begins with a thorough collection and sorting system to ensure the quality and consistency of the materials used. Start by identifying potential sources of plastic waste in your community or local area. This could include household recycling bins, local businesses, or even construction sites that might generate plastic waste.
When collecting plastic waste, it's crucial to focus on cleanliness and proper sorting. Begin by separating the plastic into different types, such as PET (polyethylene terephthalate), HDPE (high-density polyethylene), and PVC (polyvinyl chloride). Each type of plastic has its own unique properties and applications, so proper identification is essential. PET is commonly found in beverage bottles, HDPE in milk jugs and shampoo bottles, and PVC is used in pipes and electrical wiring. Ensure that all the plastic is free from contaminants like food residue, labels, and any non-plastic materials.
For household collection, encourage residents to rinse out containers and flatten them to save space. This simple step can significantly improve the quality of the collected waste. If possible, set up designated bins or containers for each type of plastic to make the sorting process more efficient. Local businesses and construction sites might have specific waste streams, so engage with them to establish a regular collection schedule.
The goal is to gather a consistent supply of high-quality plastic waste to ensure the durability and longevity of the blocks you create. By implementing a structured collection and sorting system, you'll be well on your way to producing eco-friendly blocks that can be used for various construction purposes, reducing waste and promoting sustainability. Remember, the key to success is attention to detail and a systematic approach to waste management.
Unraveling the Mystery: Can Plastic Straws Be Recycled?
You may want to see also
Cleaning: Rinse and dry plastic to remove contaminants
Cleaning and preparing recycled plastic is a crucial step before you can begin crafting your blocks. This process ensures that the plastic is free from contaminants, which can affect the quality and durability of your final product. Here's a detailed guide on how to effectively clean and prepare your plastic materials:
Rinsing Process: Begin by thoroughly rinsing the recycled plastic. This initial step is essential to remove any loose dirt, debris, or contaminants that may be present on the surface. Start by filling a large container or sink with clean water at a comfortable temperature. Submerge the plastic items in the water and use your hands or a soft brush to gently scrub the surfaces. Focus on areas that might have accumulated dirt, especially if the plastic has been exposed to outdoor elements. Rinse the plastic under running water to ensure all the cleaning agents are washed away. Pay attention to nooks and crannies, as these areas can trap contaminants.
Removing Contaminants: After rinsing, it's important to give the plastic a more thorough cleaning. Contaminants like grease, oil, or food residue can affect the bonding and strength of your blocks. Use a mild detergent or dish soap specifically designed for plastic cleaning. Apply the detergent to the plastic surfaces and let it sit for a few minutes to allow the cleaning agents to penetrate and loosen any stubborn grime. Then, rinse the plastic again, ensuring that all the detergent is removed. For a more eco-friendly approach, you can also use natural cleaning agents like vinegar or lemon juice, which are effective in cutting through grease and leaving a fresh scent.
Drying Technique: Proper drying is just as important as the cleaning process itself. Moisture can remain trapped within the plastic, leading to potential mold or mildew issues. After rinsing, gently pat the plastic with a clean towel to remove excess water. Avoid using high-pressure water or sharp objects that might scratch the surface. For larger items, consider using a fan or a hairdryer on a low setting to speed up the drying process while maintaining control over the temperature to prevent any potential damage. Ensure that the plastic is completely dry before proceeding to the next step of block-making.
By following these cleaning procedures, you'll ensure that your recycled plastic is free from contaminants, ready to be transformed into sturdy and environmentally friendly blocks. This step is a fundamental part of the process, contributing to the overall quality and longevity of your project.
Lowe's Plastic Pot Recycling: Green Gardening Practices
You may want to see also
Milling: Shred or grind plastic into small, uniform pieces
Milling is a crucial step in the process of transforming recycled plastic into building blocks. This step involves reducing the size of the plastic waste, ensuring that the final product is consistent and suitable for various applications. The goal is to create small, uniform pieces of plastic that can be further processed into blocks.
There are two primary methods for milling: shredding and grinding. Both techniques aim to break down the plastic into manageable fragments, but they differ in their approach and the resulting particle size. Shredding is often used for larger plastic items, such as bottles and containers, while grinding is more suitable for smaller pieces or flakes.
Shredding: This process involves feeding the plastic waste into a shredder, which uses sharp blades or teeth to cut and tear the material. The shredder's design can vary, with some machines using a single-stage process, where the plastic is shredded directly into the desired size. Others might employ a multi-stage system, gradually reducing the plastic's size with each pass. Shredding is effective for creating larger, coarse particles, which can then be further processed. It is commonly used in recycling facilities to prepare plastic for subsequent steps.
Grinding: Grinding is a more precise method, often used when smaller and more uniform pieces are required. This process involves feeding the plastic into a grinder, which can be a hammer mill or a granulator. The grinder's rotating blades or rollers break down the plastic, reducing it to fine particles. The goal is to create a consistent particle size, ensuring that the final product has a uniform texture. Grinding is particularly useful when the plastic needs to be combined with other materials or when creating smaller blocks for specific applications.
Both shredding and grinding require careful consideration of the plastic's type and properties. Different types of plastic have varying melting points and structural characteristics, which can affect the milling process. For instance, some plastics might require more aggressive milling to break down their molecular structure, while others may be more susceptible to heat damage during the process. Understanding the plastic's composition is essential to ensure the desired outcome.
After milling, the plastic pieces are typically sorted and cleaned to remove any contaminants. This step ensures that the final product meets the required standards and is ready for the next phase of block production. Milling is a critical process that sets the foundation for the quality and consistency of the recycled plastic blocks.
Understanding the Plastic Recycling Symbol: Does It Mean No BPA?
You may want to see also
Melting: Heat and melt plastic to a malleable state
Melting plastic to create building blocks from recycled materials is a fascinating process that requires precision and safety precautions. The first step is to gather your materials; you'll need recycled plastic, a heat source, and a mold or container to shape the blocks. Ensure the plastic is clean and dry to avoid any contaminants that could affect the melting process.
The melting process begins with a heat source. You can use a dedicated plastic melting machine or a simple heat gun. The key is to apply controlled heat to the plastic. Start by heating a small portion of the plastic at a time, as direct and intense heat can cause the plastic to melt unevenly and potentially burn. Use a heat gun or a similar tool to gently warm the plastic until it becomes soft and malleable. This process requires patience and a steady hand to avoid overheating the plastic.
As the plastic softens, it will take on a waxy, shiny appearance. At this stage, it's crucial to maintain a consistent temperature to ensure the plastic melts evenly. Keep the heat source moving to avoid scorching any specific area. Once the plastic is fully melted, it will have a smooth, fluid consistency, almost like a thick liquid. This is the ideal state for shaping your blocks.
Now, carefully pour or guide the melted plastic into your chosen mold. Ensure the mold is designed to create the desired block shape and size. You can use various molds, from simple rectangular frames to more intricate designs. Once the plastic is in the mold, quickly but gently close the mold to contain the shape. Apply gentle pressure to ensure the plastic fills the mold evenly.
After a few minutes, the plastic will start to cool and harden. Carefully open the mold to reveal your newly formed block. You might need to tap the mold gently to release the block if it doesn't come out easily. Repeat this process for each block you wish to create, ensuring you maintain consistent heating and molding techniques for uniform results. Remember, safety is paramount when working with heat, so always exercise caution and consider wearing protective gear.
The Cost of Recycling Plastic: A Deep Dive
You may want to see also
Molding: Pour melted plastic into molds to create block shapes
To create blocks from recycled plastic, molding is a crucial process that involves shaping the melted plastic into desired block forms. Here's a step-by-step guide on how to achieve this:
Materials and Preparation:
Start by gathering the necessary materials. You'll need recycled plastic flakes or pellets, a mold suitable for the block shape you desire, and a heating source. Ensure the mold is clean and dry, as any moisture can affect the plastic's adhesion. If using a custom mold, consider designing it with a release agent to facilitate easy removal of the finished block.
Melting the Plastic:
Place the recycled plastic flakes or pellets in a suitable container. Use a heat source, such as a hot plate or a dedicated plastic melting machine, to heat the plastic until it becomes molten. The temperature and duration will depend on the type of plastic; some plastics require higher temperatures and longer melting times. Stir the plastic occasionally to ensure even heating and to prevent burning.
Pouring into Molds:
Once the plastic is fully melted and homogeneous, carefully pour it into your prepared mold. Ensure the mold is level and the plastic is distributed evenly. You might need to use a spatula or a similar tool to guide the plastic into the mold, especially if the mold is complex in shape. Take note of any specific pouring techniques suggested by the mold manufacturer to achieve the best results.
Cooling and Setting:
After pouring, allow the plastic to cool and set. The cooling time will vary depending on the mold material and the desired hardness of the block. For faster results, you can use a cooling agent or place the mold in a refrigerated environment. Once set, carefully remove the block from the mold. If needed, gently tap the mold to release any remaining air bubbles.
Finishing and Customization:
At this stage, you can further customize your blocks. Sanding the edges and surfaces can improve the block's appearance and make it safer to handle. You might also consider painting or adding decorative elements to personalize your recycled plastic blocks. With proper care and maintenance, these blocks can be used for various purposes, from educational tools to decorative elements, promoting sustainability and creativity.
Sticker Removal: A Simple Step for Plastic Recycling Success
You may want to see also
Frequently asked questions
The process typically involves collecting and sorting plastic waste, cleaning and shredding the plastic into small pieces, melting and shaping the plastic into blocks, and then allowing them to cool and solidify. This method is an eco-friendly alternative to traditional building materials and can be a great way to reduce plastic waste.
Yes, certain types of plastic are more commonly used for this purpose. High-density polyethylene (HDPE) and polypropylene (PP) are popular choices due to their durability, strength, and ease of processing. These plastics are often derived from milk bottles, shampoo containers, and other household items, making them readily available for recycling.
Strength and durability can be enhanced by using a process called 'compaction' during the manufacturing stage. This involves applying pressure to the molten plastic, forcing out air bubbles and creating a more dense and homogeneous material. Additionally, adding reinforcing agents like glass fibers or other plastics can further improve the structural integrity of the blocks.