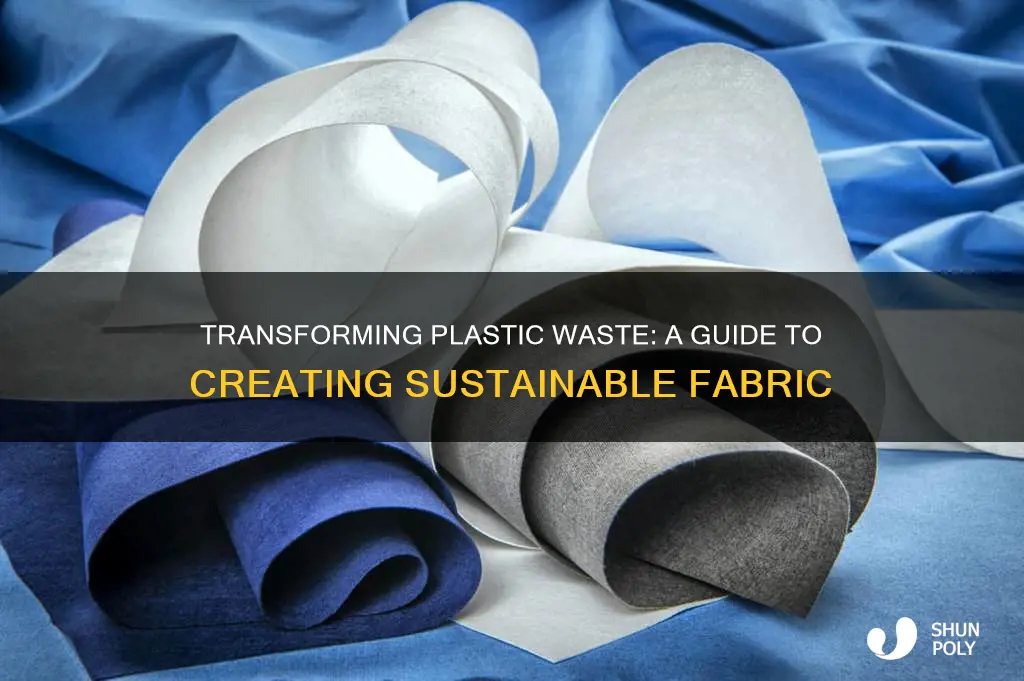
Transforming recycled plastic into fabric is an innovative process that offers a sustainable alternative to traditional textile production. This method begins with collecting and sorting plastic waste, ensuring it is free from contaminants. The plastic is then shredded into small pieces and cleaned to remove any remaining impurities. Next, the plastic flakes are melted and extruded through a spinneret, creating a continuous filament that is cooled and wound into a roll of fabric. This fabric can be further processed to create a variety of textiles, from clothing to home furnishings, offering a unique and eco-friendly material that reduces waste and promotes a circular economy.
What You'll Learn
- Sorting and Cleaning: Collect and sort plastic waste, then clean to remove contaminants
- Shredding and Grinding: Break down plastic into small pieces for further processing
- Melting and Extrusion: Heat and melt plastic, then extrude into thin strands
- Spinning and Weaving: Twist and intertwine fibers to create fabric
- Dyeing and Finishing: Apply dyes and treatments to enhance fabric's appearance and durability
Sorting and Cleaning: Collect and sort plastic waste, then clean to remove contaminants
The process of transforming recycled plastic into fabric begins with meticulous sorting and cleaning of the collected plastic waste. This initial step is crucial as it directly impacts the quality and usability of the final fabric product. Here's a detailed guide on how to effectively sort and clean plastic waste:
Collection and Sorting: Begin by gathering plastic waste from various sources, such as household recycling bins, commercial facilities, or community clean-up events. It is essential to collect a diverse range of plastic types to ensure a comprehensive recycling process. Separate the waste into different categories based on plastic types, colors, and sizes. Common plastic types include PET (polyethylene terephthalate), HDPE (high-density polyethylene), LDPE (low-density polyethylene), and PP (polypropylene). Each type has unique properties and applications in fabric manufacturing. For instance, PET is widely used in beverage bottles, while HDPE is commonly found in milk jugs. Sorting by type ensures that the recycling process can be tailored to the specific requirements of each plastic category.
Cleaning and Contaminant Removal: After sorting, the plastic waste undergoes a thorough cleaning process to eliminate contaminants and ensure the quality of the recycled material. Start by removing any non-plastic items, such as labels, caps, or other packaging, from the sorted plastic pieces. These items can interfere with the recycling process and the fabric's performance. Next, rinse the plastic waste with water to remove any remaining dirt, food residue, or labels. Use a gentle detergent or dish soap to assist in the cleaning process, ensuring that no harmful chemicals remain on the plastic. It is crucial to remove all traces of contaminants to prevent them from affecting the fabric's strength and durability. For example, food residue can lead to discoloration, while labels may contain chemicals that are not suitable for fabric production.
Advanced cleaning techniques can be employed for more effective contaminant removal. One method is using a washing machine or industrial washing equipment to scrub the plastic waste thoroughly. This process can help break down any stubborn contaminants and ensure a higher level of cleanliness. Additionally, consider using a centrifuge to separate any remaining liquids or small particles from the plastic, further enhancing the cleaning process.
Drying and Preparation: After cleaning, the sorted and cleaned plastic waste needs to be dried to remove any moisture. Spread the plastic pieces out in a well-ventilated area or use a drying rack to ensure even drying. Proper drying is essential to prevent mold growth and maintain the integrity of the plastic. Once dry, the plastic can be shredded or granulated, depending on the desired fabric structure. Shredding produces smaller pieces, which can be used for weaving or knitting, while granulation results in small, uniform pellets, suitable for spinning into fibers.
By following these sorting and cleaning procedures, you lay the foundation for successful fabric production from recycled plastic. This step ensures that the plastic waste is transformed into a usable material, ready for the next stages of the recycling process, ultimately contributing to a more sustainable and environmentally friendly fabric industry.
Unraveling the Recycling Mystery: Can Plant-Based Plastics Be Recycled?
You may want to see also
Shredding and Grinding: Break down plastic into small pieces for further processing
The process of transforming recycled plastic into fabric begins with the careful breakdown of plastic waste into smaller, manageable pieces. This initial step is crucial as it sets the foundation for the entire fabric-making process. Shredding and grinding are the primary methods employed to achieve this reduction in size.
Shredding is an effective way to break down larger plastic items, such as water bottles, into smaller fragments. This process typically involves specialized machinery designed for plastic recycling. The shredder's sharp blades cut through the plastic, reducing it to a consistent size of flakes or chips. These shredded pieces are then sorted by size, ensuring a uniform starting point for the next stage. The shredded plastic can range from fine, almost powder-like particles to larger, more substantial flakes, depending on the desired outcome and the specific requirements of the recycling facility.
Grinding, on the other hand, is a more aggressive method of size reduction. It involves using powerful machines to grind the plastic into extremely fine particles. This process is particularly useful for breaking down hard plastic materials like those found in packaging. Grinders can produce plastic particles that are almost microscopic in size, ensuring a thorough breakdown of the material. The ground plastic can then be further processed to remove any remaining impurities and create a consistent raw material for fabric production.
Both shredding and grinding require precision and control to ensure the plastic is reduced to the appropriate size without causing excessive wear and tear on the machinery. The goal is to create a uniform particle size distribution, which is essential for the subsequent steps of plastic cleaning, melting, and spinning into fibers. This initial breakdown process is a critical phase in the journey from recycled plastic to fabric, as it sets the stage for the efficient and effective transformation of waste into a valuable resource.
Recycling Plastic: Unraveling the Mystery of PRF and MRF
You may want to see also
Melting and Extrusion: Heat and melt plastic, then extrude into thin strands
The process of transforming recycled plastic into fabric begins with the careful melting and extrusion of the plastic material. This step requires precise control over temperature and pressure to ensure the plastic is heated to its melting point without burning or degrading. Specialized equipment, such as a plastic extruder, is used to melt the plastic pellets or flakes. The extruder applies heat and pressure to the plastic, softening it and allowing it to flow. The temperature and duration of the melting process depend on the type of plastic being used, with common types including PET (polyethylene terephthalate) and HDPE (high-density polyethylene).
Once melted, the plastic is extruded through a die, which shapes it into thin strands or fibers. The extrusion process involves forcing the molten plastic through a small opening, creating a continuous strand. The die's design and settings determine the thickness and diameter of the resulting fibers. Thinner strands are often preferred for fabric production as they offer a more delicate and flexible material. The extruded strands are then cooled rapidly to solidify and maintain their shape.
To achieve the desired fabric structure, multiple extrusion processes can be employed. By layering and intertwining the extruded strands, the fabric's strength and texture can be controlled. This technique allows for the creation of various fiber thicknesses and arrangements, mimicking the look and feel of traditional fabrics. The cooling process is crucial, as it sets the plastic fibers, making them rigid and ready for further processing.
After extrusion, the plastic fibers may undergo additional treatments. Cleaning and removing any impurities is essential to ensure the fabric's quality. This can be done through washing or using chemical processes. The fibers might also be stretched or oriented to improve their strength and flexibility, making them more suitable for weaving or knitting.
The melting and extrusion process is a critical phase in the recycling and fabrication of plastic into fabric. It requires technical expertise and specialized machinery to handle the heat and pressure effectively. This step transforms the recycled plastic into a usable form, setting the foundation for creating sustainable and innovative fabrics.
The Surprising Truth: How Much Recycled Plastic Really Gets Reused
You may want to see also
Spinning and Weaving: Twist and intertwine fibers to create fabric
Spinning and weaving are fundamental processes in fabric creation, and they can be applied to materials derived from recycled plastic, offering an eco-friendly approach to textile production. This method involves transforming plastic waste into fibers, which are then spun and woven to create durable and sustainable fabrics. Here's a step-by-step guide to understanding this intricate process:
Fiber Preparation: The journey begins with collecting and sorting plastic waste. Common sources include plastic bottles, bags, and packaging. These items are cleaned and shredded to create small plastic flakes. The flakes are then washed to remove any contaminants, ensuring the final product is of high quality. The next step is to melt and extrude the plastic flakes, a process that turns them into thin strands called 'plastic fibers' or 'plastic yarns'. These fibers are often quite short, and their quality depends on the initial plastic type and the extrusion process.
Spinning: Spinning is the art of twisting these individual fibers together to form a continuous strand of yarn. There are various spinning techniques, but a common method for recycled plastic fibers is called 'wet spinning'. In this process, the molten plastic is forced through a spinneret, a small orifice, creating a fiber. The fiber is then quenched in a liquid, typically water, which causes it to solidify and set its shape. The quenched fiber is then wound onto a bobbin, creating a continuous yarn. This yarn can be further processed and twisted to create different thicknesses and strengths.
Weaving: Weaving is the process of intertwining two or more sets of yarn (warp and weft) to create a fabric. For recycled plastic fabrics, the spun yarns are prepared by winding them onto warping frames, creating a long, continuous warp thread. The weft yarns are then woven through the warp using a loom. There are numerous weaving techniques, such as plain weaving, twill weaving, and satin weaving, each producing a unique fabric pattern and structure. After weaving, the fabric may undergo additional processes like dyeing, finishing, and washing to enhance its appearance and properties.
The beauty of this method lies in its sustainability and versatility. By recycling plastic waste, we can reduce environmental pollution and create a new life for these materials. The resulting fabrics can be used for various applications, from clothing and accessories to home furnishings and industrial products. This traditional spinning and weaving technique, when applied to recycled plastic fibers, showcases how ancient craftsmanship can be adapted to address modern environmental challenges.
Unraveling the Journey: From Plastic to New Life
You may want to see also
Dyeing and Finishing: Apply dyes and treatments to enhance fabric's appearance and durability
The process of transforming recycled plastic into fabric involves several crucial steps, one of which is dyeing and finishing. This stage is essential to enhance the fabric's appearance and durability, making it suitable for various applications. Here's a detailed guide on how to achieve this:
Dyeing Process:
Dyeing recycled plastic fabric is a unique process that requires specific techniques. Start by selecting the appropriate dye for your desired color. Natural dyes derived from plants or minerals can be an eco-friendly choice, but synthetic dyes are also commonly used. The dyeing process typically involves immersing the fabric in a dye bath, ensuring complete coverage. For even dye absorption, consider using a dyeing machine or a large container to facilitate the process. The duration of the dyeing process depends on the desired shade and the type of dye used. After dyeing, it is crucial to rinse the fabric thoroughly to remove any excess dye and prevent color bleeding.
Finishing Techniques:
Finishing the fabric is an art that significantly impacts its final quality. Here are some common finishing processes:
- Scouring: This step is essential to remove any impurities, oils, or residual dyes from the fabric. Scouring agents are used to clean the fabric, ensuring it is ready for further treatments.
- Rinsing and Washing: After scouring, the fabric should be thoroughly rinsed to eliminate any chemical residues. This is followed by a gentle wash to remove any remaining dirt or debris.
- Drying and Stretching: Proper drying is critical to prevent shrinkage. Air drying is recommended, and the fabric should be handled carefully to avoid distortion. Stretching the fabric on a frame can help maintain its shape and structure.
- Treating for Durability: To enhance durability, various treatments can be applied. One common method is mercerizing, which gives the fabric a lustrous appearance and improves its strength. Other treatments include singeing (removing excess fibers to make the fabric smoother) and finishing with a protective coating to repel stains and moisture.
- Gumming: This process involves applying a gum solution to the fabric's surface, providing additional strength and flexibility.
By carefully selecting dyes and employing various finishing techniques, you can create a high-quality, aesthetically pleasing fabric from recycled plastic. This process ensures that the final product is not only visually appealing but also durable and suitable for a wide range of applications, from fashion to home decor.
Uncover the Truth: Does Coles Recycle Soft Plastic?
You may want to see also
Frequently asked questions
The process begins with collecting and sorting plastic waste, which is then cleaned and shredded into small pieces. These plastic flakes are washed to remove impurities and melted into a molten state. The molten plastic is extruded through a spinneret, creating a continuous filament that is cooled and drawn to form fibers. These fibers are then woven or knitted to create fabric.
Yes, various types of plastic can be recycled into fabric, including PET (polyethylene terephthalate), HDPE (high-density polyethylene), and LDPE (low-density polyethylene). Each type of plastic has unique properties, and the choice of plastic depends on the desired characteristics of the fabric, such as strength, softness, and breathability.
Recycling plastic reduces the amount of waste sent to landfills or incinerators, preventing environmental pollution and the release of harmful greenhouse gases. It also helps conserve natural resources by reducing the need for virgin materials. By reusing plastic, we can minimize our environmental footprint and contribute to a more sustainable future.
Absolutely! Recycled plastic fabric has numerous applications, including clothing, accessories, home textiles, automotive interiors, and even outdoor gear. Its durability and versatility make it suitable for a wide range of products. Additionally, recycled plastic fabric can be blended with other materials to enhance its properties, making it a popular choice for eco-conscious consumers and manufacturers.