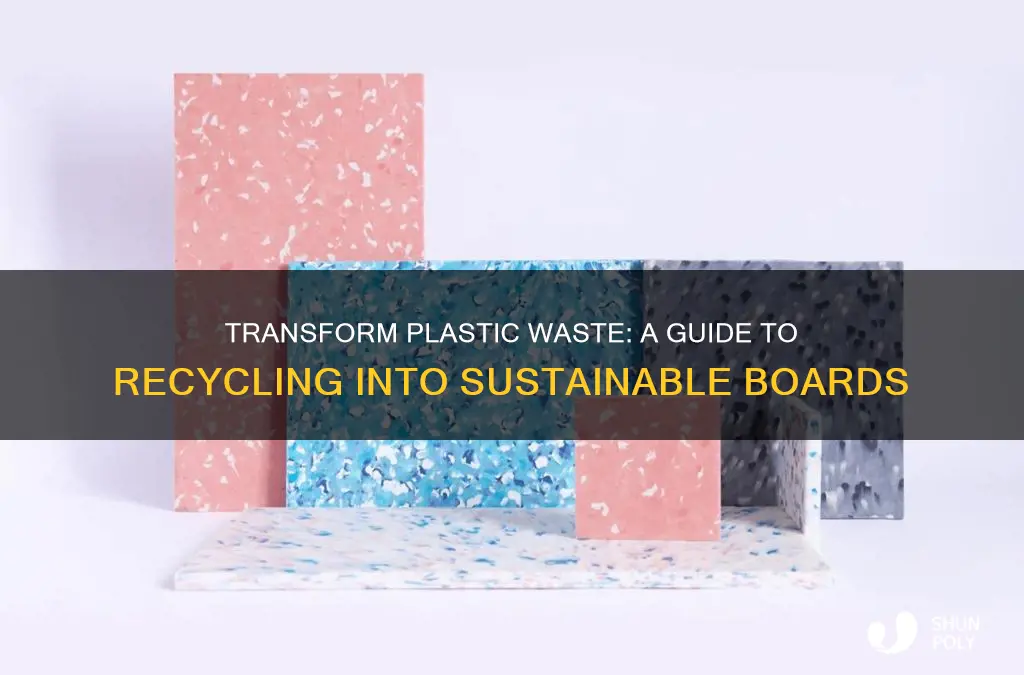
Recycling plastic into boards is an innovative process that transforms waste into valuable resources. It involves collecting and sorting plastic materials, such as PET bottles or HDPE containers, and then cleaning and shredding them into small pieces. These plastic flakes are further processed through a melting and molding process to create various types of boards, including rigid plastic boards, foam boards, and even composite boards. This method not only reduces plastic waste but also provides a sustainable alternative to traditional wood products, making it an eco-friendly choice for construction, packaging, and various industrial applications.
What You'll Learn
- Collection and Sorting: Gather and sort plastic waste by type and color for efficient recycling
- Cleaning and Shredding: Clean and shred plastic to reduce size and prepare for processing
- Melting and Molding: Melt plastic and mold it into board shapes using heat and pressure
- Cooling and Cutting: Cool and cut boards to desired thickness and size
- Finishing and Sanding: Smooth and finish boards with sanding and polishing techniques
Collection and Sorting: Gather and sort plastic waste by type and color for efficient recycling
The process of recycling plastic into boards begins with a crucial step: efficient collection and sorting of plastic waste. This initial phase is fundamental to the success of the entire recycling process, ensuring that the materials are properly managed and prepared for transformation. Here's a detailed guide on how to approach this stage:
Collection: Begin by establishing a comprehensive waste collection system. This involves setting up designated collection points or bins in various locations, such as homes, offices, schools, and public spaces. Educate the community or users about the importance of proper waste segregation at the source. Encourage people to separate their plastic waste into different categories, such as bottles, containers, packaging, and film plastics. Providing clear guidelines and instructions on what to collect and how to prepare the waste will significantly improve the quality of the sorted material.
Sorting Process: Once the plastic waste is collected, the next step is to sort it systematically. This process requires attention to detail and organization. Sort the plastic items by type, which includes identifying different types of plastics such as PET (polyethylene terephthalate), HDPE (high-density polyethylene), PVC (polyvinyl chloride), LDPE (low-density polyethylene), and PP (polypropylene). Each type of plastic has unique properties and applications in the recycling process. For instance, PET is commonly used for beverage bottles and can be recycled into fibers for clothing or new bottles. HDPE is often found in milk jugs and shampoo bottles and can be recycled into various products.
Color sorting is another critical aspect of this stage. Plastic items can be sorted by color to ensure that the final product meets specific requirements or market demands. For example, white or clear plastics are often preferred for certain applications, while colored plastics might be suitable for other uses. Sorting by color also helps in creating a more uniform and aesthetically pleasing final product.
To facilitate the sorting process, consider using color-coded bins or containers. Clearly label each bin with the type of plastic it should hold, making it easier for volunteers or staff to sort the waste efficiently. This methodical approach ensures that the plastic waste is organized and ready for the next phase of recycling, where it will be processed into boards or other useful products.
By implementing a well-organized collection and sorting system, you lay the foundation for a successful plastic recycling program. This step is essential to maintain the quality and purity of the recycled material, ultimately leading to the production of high-quality boards or other plastic-derived products. It also ensures that the recycling process is efficient, cost-effective, and environmentally friendly.
Unraveling the Mystery: Can Plastic Knives Be Recycled?
You may want to see also
Cleaning and Shredding: Clean and shred plastic to reduce size and prepare for processing
The process of recycling plastic into boards begins with thorough cleaning and shredding, which are crucial steps to ensure the quality and efficiency of the final product. Cleaning is an essential first step to remove any contaminants and impurities that may be present on the plastic. This includes removing labels, caps, and any non-plastic materials that could interfere with the recycling process. Start by sorting the plastic waste into different categories based on their type and color. This initial sorting helps in identifying and removing any hazardous materials or items that might pose a risk during processing.
Once sorted, the plastic needs to be cleaned to eliminate dirt, grime, and any residual contaminants. This can be achieved through various methods such as washing the plastic with warm soapy water or using specialized cleaning agents. For effective cleaning, ensure that the plastic is thoroughly rinsed to remove any soap residue. After cleaning, it is important to dry the plastic completely to prevent moisture-related issues during shredding. Air drying or using a industrial-grade dryer can be employed for this purpose.
Shredding is the next critical step in reducing the size of the plastic waste. This process involves breaking down the plastic into smaller pieces, making it easier to handle and process. Industrial shredders are commonly used for this task as they can handle large volumes of plastic efficiently. The shredded plastic should be of a consistent size to ensure uniform processing. Aim for a size range that is suitable for the specific board-making process you have in mind. For example, if you plan to create large-format boards, a larger shred size might be preferable.
During the shredding process, it is important to maintain a clean and organized work environment. Proper safety equipment, such as gloves and eye protection, should be worn to prevent any injuries. Additionally, ensure that the shredder is properly maintained and lubricated to avoid mechanical issues and potential damage. After shredding, the plastic flakes can be further sorted and classified based on their quality and color, which is an important step for high-quality board production. This initial cleaning and shredding process lays the foundation for the subsequent stages of recycling, where the plastic will be transformed into valuable boards.
Unveiling the Secrets: Paper and Plastic Recycling Methods
You may want to see also
Melting and Molding: Melt plastic and mold it into board shapes using heat and pressure
The process of recycling plastic into boards involves a technique known as melting and molding, which utilizes heat and pressure to transform plastic waste into solid, usable board materials. This method is an effective way to recycle plastic and create new products, especially for those seeking to upcycle plastic waste into functional items. Here's a detailed guide on how to achieve this:
Melting Process: Begin by gathering your plastic waste, ensuring it is clean and sorted by type if possible. Common types of plastic used for this process include polypropylene (PP), high-density polyethylene (HDPE), and polystyrene (PS). These plastics are often chosen due to their ease of melting and molding. Cut or shred the plastic into small, uniform pieces to facilitate even melting. Place the plastic pieces in a specialized melting machine or a custom-built oven designed for plastic recycling. The melting temperature varies depending on the type of plastic, but typically, temperatures between 200°C and 300°C (392°F to 572°F) are used. This heat will soften the plastic, allowing it to be molded into new shapes. It's crucial to monitor the melting process to ensure the plastic doesn't burn or degrade.
Molding and Pressing: Once the plastic is melted, it's time to mold it into board shapes. This step requires precision and the right equipment. You'll need a mold, which can be custom-made to create the desired board dimensions and patterns. The mold should be heated to a temperature slightly above the melting point of the plastic to facilitate the molding process. Pour the molten plastic into the mold, ensuring it's filled evenly. Apply heat and pressure to the mold using a hydraulic press or a similar mechanism. The pressure and temperature will depend on the specific requirements of your board design. For example, you might need to apply pressure to create a solid, flat board or use less pressure for more intricate designs. Allow the plastic to cool and solidify within the mold, and then carefully remove it.
This method of recycling plastic into boards is an eco-friendly alternative to traditional manufacturing processes, reducing waste and providing a sustainable solution for plastic upcycling. It allows for creativity in design, as you can create various board sizes, thicknesses, and patterns by adjusting the molding process. Additionally, this technique can be scaled up for commercial applications, making it a viable option for businesses looking to incorporate recycled materials into their products.
Eco-Friendly Guide: Recycling Amazon's Plastic Packaging
You may want to see also
Cooling and Cutting: Cool and cut boards to desired thickness and size
To effectively recycle plastic into boards, proper cooling and cutting techniques are essential. This process ensures the material is manageable and allows for precise shaping and sizing. Here's a detailed guide on how to achieve this:
Cooling the Plastic:
After the plastic has been melted and formed into sheets or panels, it needs to be cooled rapidly and evenly. This step is crucial as it determines the final properties of the board. Start by placing the plastic sheets in a controlled cooling environment, such as a refrigerated room or a cooling tunnel. Maintain a consistent temperature throughout the cooling process to avoid uneven cooling, which can lead to warping or cracking. The cooling time will vary depending on the thickness and size of the plastic sheets, but it typically ranges from a few hours to overnight. Regularly monitor the temperature and adjust as needed to ensure optimal cooling.
Cutting the Boards:
Once the plastic boards are cooled and hardened, they can be cut to the desired thickness and size. Here's a step-by-step approach:
- Select the Cutting Tool: Use a sharp, specialized cutting tool designed for plastic. A hot knife or a precision laser cutter is ideal for this purpose. These tools provide clean, precise cuts without causing excessive heat, which can distort the plastic.
- Mark the Cutting Lines: Carefully measure and mark the desired dimensions on the plastic board. Ensure the markings are accurate to achieve the required thickness and shape.
- Make the Cuts: Position the cutting tool along the marked lines and apply gentle pressure. Move the tool slowly and steadily to make clean cuts. For intricate designs or curves, consider using a computer-controlled cutting machine for precision.
- Deburr and Smoothen: After cutting, inspect the edges for any roughness or burrs. Use a fine-grit sandpaper or a deburring tool to smoothen the edges, ensuring a professional finish.
- Quality Check: Examine the cut boards for any defects or imperfections. Check for straight cuts, consistent thickness, and overall quality. This step is crucial to ensure the final product meets the desired standards.
By following these cooling and cutting procedures, you can transform recycled plastic into high-quality boards, ready for various applications, from construction to furniture making. Proper cooling ensures the plastic remains stable, while precise cutting techniques guarantee the desired outcome. This process is a critical part of the recycling and repurposing journey, allowing for the creation of sustainable and innovative products.
Reusing Plastic Film: A Guide to Eco-Friendly Recycling
You may want to see also
Finishing and Sanding: Smooth and finish boards with sanding and polishing techniques
When it comes to recycling plastic into boards, the finishing and sanding process is crucial to achieving a smooth and professional-looking surface. This step involves refining the texture and appearance of the plastic boards to make them suitable for various applications. Here's a detailed guide on how to approach this process:
Sanding Techniques: Start by selecting the appropriate sandpaper for your project. For plastic boards, a fine-grit sandpaper, typically in the range of 120 to 220 grit, is recommended. This grit size will help remove any visible imperfections and create a relatively smooth surface. Begin sanding with gentle, even strokes, ensuring that you cover the entire board's surface. Work in small sections to maintain control and avoid overwhelming the material. As you progress, gradually increase the grit size to 240 or 320 grit for an even smoother finish. This step is essential to prepare the boards for the final polishing stage.
Polishing for a Smooth Surface: After sanding, the boards will benefit from a thorough polishing process. This step enhances the surface's smoothness and adds a subtle shine. You can use a variety of polishing compounds or waxes designed for plastic materials. Apply a small amount of the chosen polish to a clean cloth and gently rub it across the board's surface in the direction of the grain. For best results, work in small sections, ensuring that you cover the entire board. Allow the polish to dry slightly, then buff the surface with a clean, dry cloth to achieve a high-gloss finish. This step is key to making the recycled plastic boards aesthetically pleasing.
Refining Edges and Corners: Pay close attention to the edges and corners of the boards during the sanding and polishing process. These areas often require additional care due to their unique shape and exposure. Use a finer grit sandpaper, such as 400 or 600 grit, to carefully refine the edges, ensuring a smooth transition between the board's surface and the edges. For corners, consider using a corner-rounding tool to create a gentle, rounded edge, which adds a refined touch to the overall appearance.
Multiple Passes for Consistency: Consistency is key when sanding and polishing plastic boards. It's essential to make multiple passes in the same direction to ensure an even finish. This technique helps remove any scratches or imperfections left by previous sanding stages. Take your time and be patient, as rushing this step may lead to an uneven surface. Remember, the goal is to create a seamless transition between the different grits of sandpaper and achieve a polished, professional look.
Final Inspection and Touch-Ups: Once you've completed the sanding and polishing, conduct a thorough inspection of the boards. Look for any remaining imperfections or uneven spots and address them with additional sanding or polishing. This step ensures that the final product meets your desired quality standards. Additionally, consider applying a protective coating or sealant to enhance the boards' durability and appearance, especially if they will be used in outdoor or high-traffic environments.
Does DC Recycle Plastic 5? Unveiling the Truth
You may want to see also
Frequently asked questions
The process typically involves collecting and sorting plastic waste, cleaning and shredding it, melting the plastic into a molten state, and then shaping it into flat sheets or boards. This can be done through various methods like extrusion or compression molding.
Not all plastics are ideal for this process. Common types used for board production include high-density polyethylene (HDPE), polypropylene (PP), and polystyrene (PS). These plastics are chosen for their durability, strength, and ease of processing.
You can play a part by properly disposing of plastic waste, ensuring it is clean and dry. Support local recycling initiatives and choose products made from recycled plastic. Also, consider purchasing products that use recycled boards, promoting the demand for this sustainable material.
Recycling plastic reduces the amount of waste sent to landfills, preventing potential soil and water pollution. It also conserves natural resources, as it uses recycled materials instead of virgin resources. This process helps lower energy consumption and greenhouse gas emissions associated with manufacturing new plastic products.