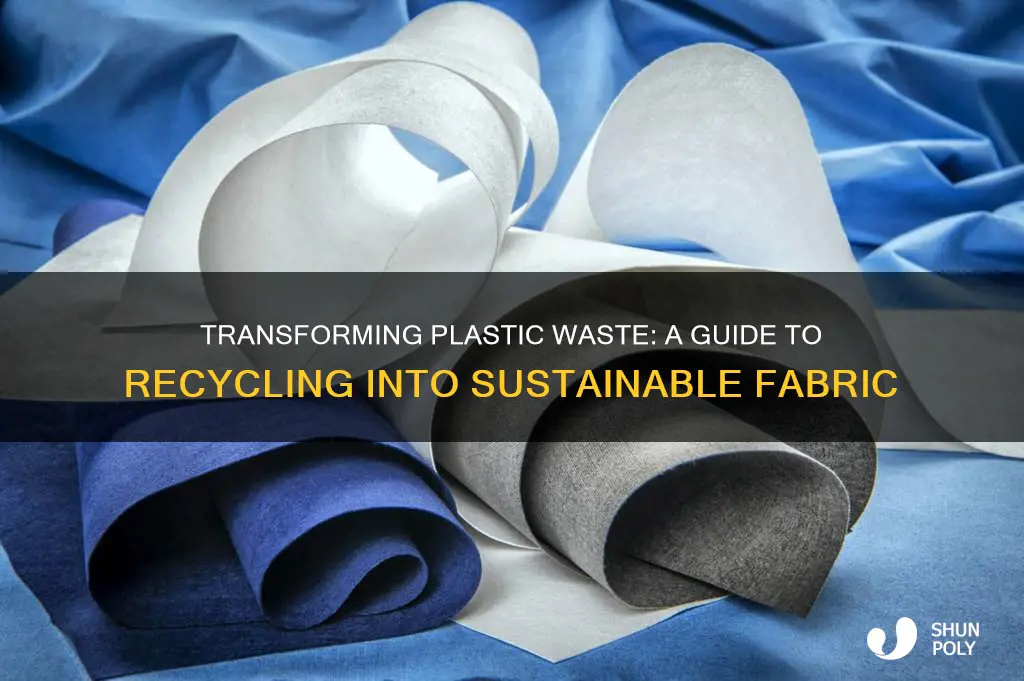
Recycling plastic into fabric is an innovative process that transforms waste into a valuable resource. By breaking down plastic waste, typically through chemical or mechanical processes, it can be converted into fibers that are then woven or knitted into textiles. This method not only reduces the amount of plastic waste in landfills and oceans but also provides an eco-friendly alternative to traditional fabrics, offering a sustainable solution to the growing demand for textiles while promoting a circular economy.
What You'll Learn
- Collection and Sorting: Gather and categorize plastic waste by type and color for efficient recycling
- Cleaning and Shredding: Remove contaminants and grind plastic into small pieces for further processing
- Chemical Treatment: Use solvents to break down plastic into monomers, which can be reformed into fibers
- Spinning and Weaving: Transform plastic fibers into fabric through spinning and weaving techniques
- Dyeing and Finishing: Apply dyes and treatments to enhance fabric appearance and durability
Collection and Sorting: Gather and categorize plastic waste by type and color for efficient recycling
The process of recycling plastic into fabric begins with a crucial step: efficient collection and sorting of plastic waste. This initial phase is fundamental to the success of the entire recycling project, ensuring that the materials are properly prepared for transformation into new products. Here's a detailed guide on how to approach this stage:
Collection: The first step is to gather plastic waste from various sources. This can include household items like water bottles, milk jugs, and packaging materials, as well as industrial and commercial plastic waste. It is essential to collect a diverse range of plastic types to ensure a broader recycling capacity. Set up designated collection points in communities, offices, or industrial areas, clearly labeled for different types of plastics. For instance, you can have separate bins for PET (polyethylene terephthalate) bottles, HDPE (high-density polyethylene) containers, and LDPE (low-density polyethylene) bags. Encouraging people to separate their plastic waste at the source will significantly streamline the recycling process.
Sorting: Once the collection is complete, the next critical step is sorting. Proper sorting ensures that the plastic materials are recycled efficiently and effectively. Begin by separating the plastics into broad categories: PET, HDPE, LDPE, and others like PVC or PS. This initial sorting can be done manually or with the help of automated systems. For instance, near-infrared (NIR) spectroscopy can be employed to identify different plastic types based on their molecular structure. After initial sorting, further categorize the plastics by color. This color-coding system is essential for creating specific fabric colors or patterns. For example, clear PET bottles can be sorted into a 'clear' category, while green milk jugs can be set aside for a 'green' fabric application.
Color sorting can be done manually or with the aid of color-sorting machines, which use advanced technology to identify and separate plastics based on hue. This level of organization is vital as it allows for the creation of unique and consistent fabrics. By categorizing the plastics by type and color, you are essentially preparing the materials for their specific recycling paths, ensuring that the end product meets the desired specifications. This meticulous sorting process is a key factor in the success of recycling plastic into fabric, as it sets the foundation for high-quality, consistent output.
Unveiling America's Plastic Recycling Reality: A Comprehensive Overview
You may want to see also
Cleaning and Shredding: Remove contaminants and grind plastic into small pieces for further processing
The initial step in recycling plastic into fabric is crucial for ensuring the quality and safety of the final product. Cleaning and shredding are essential processes that involve removing contaminants and reducing plastic into smaller pieces, which are then ready for further processing.
Cleaning Process:
Begin by sorting the plastic waste to separate different types of plastics, as this will influence the cleaning method. For instance, PET (polyethylene terephthalate) and HDPE (high-density polyethylene) are commonly used in beverage bottles and can be cleaned using different techniques. Start by rinsing the plastic waste with water to remove any visible dirt or debris. This initial cleaning step is vital to prevent contamination during the recycling process. Use a high-pressure water jet or a mechanical wash system to ensure thorough cleaning. For more stubborn contaminants, consider using a chemical cleaner specifically designed for plastic recycling. These chemicals can help dissolve and remove any remaining impurities. After cleaning, thoroughly rinse the plastic to eliminate any chemical residues.
Shredding and Grinding:
Once the cleaning process is complete, the plastic material needs to be shredded or ground into small, uniform pieces. This step is crucial as it prepares the plastic for the subsequent stages of recycling. Shredding machines are commonly used to reduce the plastic waste into thin strips or flakes. The size of the shredded pieces will depend on the desired end product. For example, if you aim to create a fabric with a specific texture, you might want to adjust the shredding size accordingly. After shredding, the plastic flakes can be further processed by grinding them into even smaller particles. This grinding process ensures that the plastic is in a form suitable for spinning or weaving into fibers. Grinding machines can produce particles of various sizes, allowing for customization based on the recycling method and the desired fabric characteristics.
It is important to maintain a clean and controlled environment during the cleaning and shredding process to minimize the risk of cross-contamination. Proper waste management and disposal of any hazardous materials used in cleaning are essential to ensure a safe and efficient recycling process.
Transform Old Banners: Creative Recycling Ideas for Plastic Materials
You may want to see also
Chemical Treatment: Use solvents to break down plastic into monomers, which can be reformed into fibers
The process of recycling plastic into fabric through chemical treatment involves a series of intricate steps that require careful handling of chemicals and specialized equipment. This method is particularly effective for transforming various types of plastic waste into valuable textile materials. Here's an in-depth look at the chemical treatment process:
Solvent Selection and Preparation: The first crucial step is choosing the right solvent. Common solvents used in this process include acetone, methylene chloride, and various alcohol-based solutions. These solvents are carefully selected based on their ability to dissolve and break down specific types of plastic polymers. For instance, acetone is often used for polypropylene, while methylene chloride can be effective for polystyrene. The solvent is prepared by diluting it with water or other carriers to achieve the desired concentration, ensuring both effectiveness and safety.
Plastic Waste Preparation: Before the chemical treatment, plastic waste must be sorted and prepared. This involves cleaning and sorting the plastic materials to ensure they are free from contaminants like dirt, labels, and non-plastic components. The plastic is then shredded or granulated to create a uniform size of plastic particles, which is essential for consistent chemical treatment.
Chemical Reaction and Monomer Formation: In this stage, the prepared plastic waste is exposed to the chosen solvent under controlled conditions. The solvent acts as a powerful tool, breaking down the complex plastic polymers into their constituent monomers. For example, polyethene terephthalate (PET), commonly found in beverage bottles, can be converted into terephthalic acid and ethylene glycol monomers. This process typically requires heat and agitation to facilitate the chemical reaction, ensuring the plastic's transformation into a usable form.
Monomer Purification and Reformation: After the chemical reaction, the resulting monomers need to be purified to remove any impurities or byproducts. This purification step ensures the quality and purity of the monomers, which is crucial for the subsequent fiber formation. The purified monomers are then carefully reformed into fibers through a process called polymerization. This involves heating the monomers and applying mechanical force to create long, continuous fibers, similar to those used in textile manufacturing.
Fiber Spinning and Textile Production: The reformed fibers are now ready to be spun into yarns and eventually woven or knitted into fabrics. This stage involves specialized machinery that draws out the fibers, aligns them, and twists them together to form strong, cohesive yarns. These yarns can then be processed further to create various textile products, such as clothing, home furnishings, and industrial materials. The entire process, from chemical treatment to textile production, showcases the remarkable transformation of plastic waste into high-quality, sustainable fabrics.
Walmart's Plastic Recycling Policy: What You Need to Know
You may want to see also
Spinning and Weaving: Transform plastic fibers into fabric through spinning and weaving techniques
The process of recycling plastic into fabric involves transforming plastic waste into a usable material through spinning and weaving techniques. This method not only reduces plastic waste but also creates a sustainable and eco-friendly fabric. Here's a detailed guide on how to achieve this:
Spinning Plastic Fibers:
Start by collecting and sorting plastic waste, ensuring it is clean and free from contaminants. Common plastic types used for recycling include PET (polyethylene terephthalate) and HDPE (high-density polyethylene). The plastic is then shredded or granulated to create small plastic flakes. These flakes are further processed to produce plastic fibers. One common method is melt-spinning, where the plastic is heated and extruded through a spinneret, a device with tiny holes, creating thin fibers. These fibers are then cooled and collected, forming the basis of your recycled fabric.
Preparing the Fibers:
After spinning, the plastic fibers need to be treated and prepared for weaving. This includes cleaning and conditioning the fibers to ensure they are strong and flexible. One technique is to use a process called 'wet-spinning,' where the fibers are exposed to a liquid, often a solvent, which helps in aligning the polymer chains, making the fibers more durable. The fibers are then dried and sometimes treated with chemicals to enhance their properties.
Weaving Technique:
Weaving is an ancient craft that can be utilized to transform the plastic fibers into a fabric structure. Here's a simplified process:
- Setting Up: Prepare a loom or weaving frame, ensuring it is the correct size for your desired fabric dimensions.
- Warping: Create a warp, which is the lengthwise thread on the loom. You can use a continuous filament yarn made from the same plastic material for strength.
- Weaving: Take the spun and treated plastic fibers and interlace them with the warp. You can experiment with different weaving patterns like plain, twill, or satin weaves. Each pattern will give the fabric a unique appearance and feel.
- Finishing: Once the weaving is complete, carefully remove the fabric from the loom. The fabric may require additional processing, such as washing, drying, and stretching, to ensure it is soft and flexible.
This traditional weaving method allows for the creation of a strong and durable fabric with a unique texture, all while utilizing recycled plastic materials. The process can be adapted to create various fabrics, from lightweight textiles to heavier-duty materials, depending on the desired application.
By employing these spinning and weaving techniques, you can effectively recycle plastic into a functional and sustainable fabric, contributing to a more circular economy and reducing the environmental impact of plastic waste.
Mastering Plastic Recycling: A Comprehensive Guide to Calculating Rates
You may want to see also
Dyeing and Finishing: Apply dyes and treatments to enhance fabric appearance and durability
The process of transforming recycled plastic into fabric involves several steps, and one crucial aspect is dyeing and finishing to achieve the desired appearance and durability. Here's an overview of this process:
Dyeing Process:
When recycling plastic into fabric, the initial step is to dye the material to create a visually appealing and unique product. This process can be achieved through various methods, such as solution dyeing or yarn dyeing. In solution dyeing, the plastic fibers are dyed in a liquid bath, allowing for an even and consistent color. This method is particularly useful for creating vibrant and long-lasting colors. Alternatively, yarn dyeing involves dyeing the individual fibers before spinning them into yarn, resulting in a more textured and varied color effect. The choice of dyeing technique depends on the desired outcome and the specific requirements of the project.
Color Selection and Preparation:
Before dyeing, it is essential to select the right dyes and pigments that will adhere to the plastic fibers effectively. Different dyes have varying levels of solubility and affinity for plastic, so choosing the appropriate ones is crucial. The preparation process involves mixing the dyes with solvents or other carriers to create a consistent and evenly dispersed solution. This step ensures that the dye is applied uniformly across the fabric, resulting in a vibrant and long-lasting colorfast appearance.
Application Techniques:
There are several methods to apply dyes to the recycled plastic fabric. One common technique is the immersion dyeing process, where the fabric is submerged in the dye bath, allowing the color to penetrate the fibers. This method is suitable for creating solid and uniform colors. For more intricate designs or patterns, techniques like tie-dye or screen printing can be employed, offering a range of creative possibilities. The application process requires precision and control to ensure the desired color distribution and intensity.
Finishing Treatments:
After dyeing, various finishing treatments can be applied to enhance the fabric's appearance and durability. One common treatment is washing to remove excess dyes and impurities, ensuring a clean and refined look. This process can also help fix the dye to the fibers, improving colorfastness. Additionally, treatments like scumming or scouring can be used to remove any surface impurities and prepare the fabric for further processing. These finishing steps contribute to the overall quality and appeal of the recycled plastic fabric.
Durability and Weather Resistance:
To ensure the fabric's durability, additional treatments can be applied. This includes processes like heat setting, which permanently sets the dye and adds strength to the fibers. Water-repellent treatments can also be incorporated to enhance the fabric's resistance to moisture, making it suitable for outdoor applications. These finishing touches are essential to guarantee that the recycled plastic fabric can withstand various environmental conditions and everyday wear and tear.
Unraveling the Mystery: Do You Need to Remove Labels from Plastic for Recycling?
You may want to see also
Frequently asked questions
The process typically involves several steps. First, plastic waste, such as bottles or packaging, is collected and sorted. Then, it is cleaned and shredded into small pieces called flakes. These flakes are washed to remove contaminants and then melted into a molten state. The molten plastic is extruded through a spinneret, creating a continuous filament. This filament is then cooled and drawn to create a thin strand, which is further processed to form a fabric-like material. Finally, the fabric is woven or knitted to create a usable product.
Yes, there are various methods employed in the recycling process. One common method is called 'chemical recycling' or 'solvent-based recycling'. This process uses chemicals to break down the plastic into its original monomers, which can then be repolymerized into new plastic fibers. Another approach is mechanical recycling, where the plastic is physically transformed without altering its chemical structure. This often involves shredding, washing, and re-pelletizing the plastic to create new fibers.
Recycling plastic into fabric offers several advantages. It helps reduce plastic waste that often ends up in landfills or pollutes the environment. By reusing plastic, we can conserve natural resources and decrease the demand for virgin materials. This process also reduces energy consumption compared to producing new fabrics from raw materials. Additionally, recycled plastic fabrics can be durable, lightweight, and breathable, making them suitable for various applications, including clothing, home textiles, and automotive interiors.