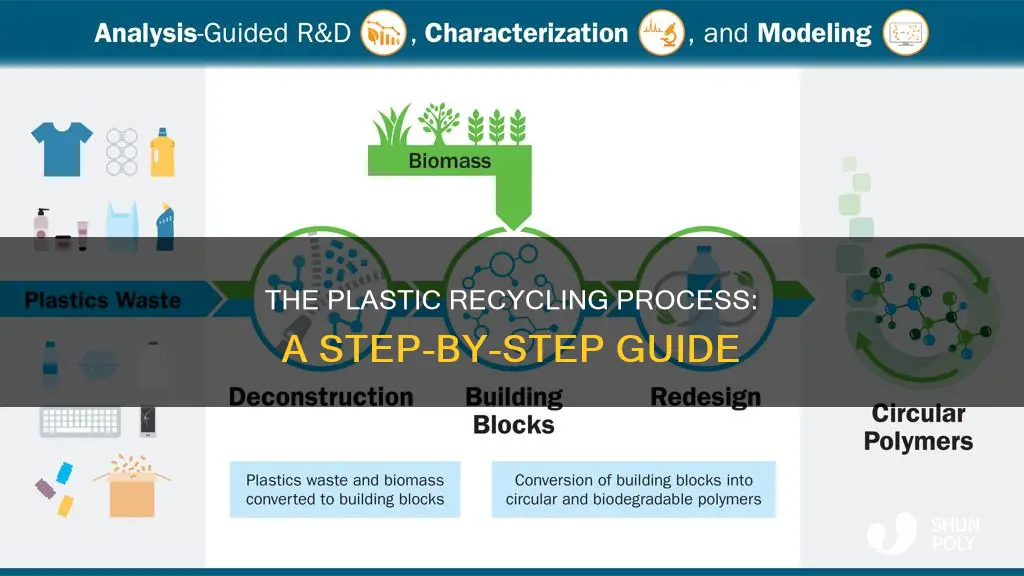
Plastic recycling is the process of sorting and shredding plastic waste to create new products. The purpose of recycling plastic is to reduce pollution and eliminate plastics from the environment, which can cause animal fatalities, health concerns, and other issues. The process also reduces fossil fuel usage, as plastic is made from crude oil, and creates employment opportunities. The first step in the recycling process is the collection of plastic waste from homes and institutions. The plastic is then sorted, shredded, washed, and melted down to form pellets, which are then moulded into new products. While plastic recycling is important, it is also important to be aware of greenwashing, where corporations may exaggerate the environmental benefits of their recycling processes.
Characteristics | Values |
---|---|
Purpose | To benefit the environment, ecosystems, and human life |
Benefits | Reduces pollution, fossil fuel usage, and waste |
Collection | Recycling containers in public places, homes, and institutions |
Sorting | By color, thickness, or resin type; manual and automatic |
Cleaning | Removal of impurities like dirt and organic residue |
Shredding | Shredding into flakes or pellets |
Melting | Melt processing to form pellets |
Moulding | Moulded into new products |
Demand | Requires demand for recycled products |
What You'll Learn
Sorting plastic from other materials
One initial step in sorting plastic involves separating it from other types of waste, such as non-recyclable materials, large items like pots and pans, and unsuitable materials like wood. This can be done manually by trained human pickers or through the use of technology such as reverse vending machines or cameras on sorting lines that can identify specific types of plastic. Some facilities use trommel screens, which are large, inclined, rotating, cylindrical sieves that separate materials based on size, allowing smaller pieces of plastic to fall through while larger items are separated.
Once the plastic has been separated from other types of waste, it needs to be sorted into different streams based on the type of plastic. This can be done through a variety of methods, including fluorescent markers, watermarks, or codes that are invisible to the naked eye but can be read by cameras on the sorting line. These codes can be embossed into the plastic or integrated into printed labels, allowing sorting equipment to identify the type of plastic and separate it accordingly.
After the initial sorting process, the plastic is typically shredded or melted into small pieces called "flake." This step helps to further separate different types of plastic, as some plastics float while others sink. It also removes any remaining contaminants, such as small pieces of metal or glass. The flake is then washed, dried, and processed into pellets, which can be used to create new products.
It's important to note that some plastics are not suitable for traditional recycling methods and are instead processed through incineration or sent abroad for recycling. Additionally, the design of packaging can impact the sorting process, as some plastics with multiple layers or certain colours may be more difficult or expensive to separate and recycle.
The Plastic Machine: A Guide to Recycling and Reusing
You may want to see also
Reprocessing plastic into pellets
Plastic pelletizing is a crucial process in the recycling industry that involves converting plastic waste into small, cylindrical pellets, also known as granules. This process is essential in reducing the environmental impact of plastic pollution by providing a systematic and efficient way to recycle various plastic materials.
The recycling process begins with sorting the plastic waste into three streams: the intended plastic (high value), missorted plastic containers (medium value), and waste (negative value). The sorted plastic is then baled into compressed 1000-1500 lb rectangular blocks and sold to recyclers. The bales are then cut apart and pushed onto a conveyor belt for further processing.
To make recycled plastic pellets, the waste plastic undergoes a series of steps. Firstly, a crusher or grinder is used to break down the plastic into small pieces or flakes. These flakes are then washed in hot water and detergent to remove dirt and adhesives. The flakes are rinsed again and air-dried to ensure no residual contaminants remain.
The clean flakes are then fed into a plastic pellet making machine, also known as an extruder. Within the machine, the plastic is mixed and re-plasticized under high temperature and pressure, creating a viscous flow. The molten plastic is then extruded through a die and cut into strands or directly into pellets using a pelletizing machine or cutter.
The resulting pellets are cooled rapidly using a water bath or dry ice to solidify them. Finally, the pellets are separated from the water, dried, and packaged for storage or use. These recycled plastic pellets have a wide range of applications across various industries, including packaging, construction, automotive, textiles, and electronics.
The Cleaning Process of Recycled Plastic Unveiled
You may want to see also
Mechanical recycling
The process of mechanical recycling begins with the collection of plastic waste from homes, businesses, and recycling centres. This plastic waste is then sent to Material Recovery Facilities (MRFs), which handle plastic and non-plastic materials, or Plastic Recovery Facilities (PRFs), which handle just plastic. At these facilities, the plastic waste is sorted into different types of plastic using various techniques and equipment, such as sink/float separators, manual picking, and trommels.
After the initial sorting process, the plastic is shredded into smaller pieces, washed to remove dust, dirt, and any traces of food or drink, and then sorted again based on colour, thickness, or distinguishable densities of different polymers. This step ensures that the plastic is clean and ready for the next stage of the process.
The washed and sorted plastic flakes are then processed through extruders, where they are melted, filtered, and granulated into pellets or nurdles. These pellets are then used to manufacture new products, such as tiles, fridges, freezers, or even new plastic products. The specific process and additional steps may vary depending on the intended application and the quality of the plastic.
The Plastic Recycling Myth: What Really Happens to Our Waste?
You may want to see also
Chemical recycling
There are several chemical recycling technologies, including pyrolysis, gasification, hydro-cracking, depolymerisation, and dissolution. Pyrolysis is a process in which plastics are heated to high temperatures in an oxygen-free environment, resulting in a liquid mix of various compounds called pyrolysis oil. Pyrolysis oil contains large amounts of olefins, which are simple hydrocarbons that are essential building blocks for today's chemicals and polymers. By using pyrolysis, chemical manufacturers can produce olefins in a much less energy-intensive process compared to traditional methods like steam cracking.
Another chemical recycling technique is depolymerisation, which breaks down plastics into their fundamental building blocks or monomers. This process can be applied to 'condensation' polymers such as polyester, polystyrene, and polyamides, yielding either single-monomer molecules or shorter polymer fragments known as oligomers. The resulting monomers are identical in quality to virgin monomers, allowing for the creation of new polymers that are similar in quality to the originals.
The adoption of chemical recycling requires further investments and a strong policy framework. However, with the right support, chemical recycling has the potential to significantly reduce plastic waste and create a more sustainable future for the industry.
The Surprising Truth About Plastic Recycling
You may want to see also
Wet separation
The wet separation process is just one of many methods used to separate plastic materials. Other techniques include manual picking, where large items, non-recyclables, and obvious contaminants are removed by hand, and trommels, which are cylindrical drums with holes that allow finer materials to fall through. Optical sorting machines, which can distinguish between different types of plastics, are also used, along with magnetic and Eddy current separators to remove metal contaminants.
In addition to wet separation, advanced technologies such as fluorescence, electrostatics, infrared, and near-infrared (NIR) spectroscopy are employed to identify and separate different types of plastics and other materials. NIR spectroscopy, for instance, can effectively differentiate between biodegradable plastics (e.g., PLA, PBAT) and conventional plastics (e.g., PE, PET). However, NIR sorting technology may struggle with transparent and dark plastics, potentially leading to misclassification.
Overall, the wet separation process is an essential step in plastic recycling, enabling the separation of plastics by density. This process is complemented by other sorting and separation techniques to ensure effective recycling and contribute to environmental sustainability.
Florida's Plastic Straws: Are They Recyclable?
You may want to see also
Frequently asked questions
Collection is the first step in recycling plastic. The more plastic is collected, the more material there will be for the recycling process. Individuals can contribute by depositing their used plastic into recycling containers, ensuring they separate common waste from plastic waste materials.
The plastic is then sorted and shredded into flakes or pellets. Sorting is done automatically with a manual sort to ensure all contaminants have been removed. The flakes are then washed in hot water and detergent to remove surface dirt and dissolve adhesives.
A wide range of products can be made from recycled plastic, including bottles, fleece jackets, detergent bottles, and even high-end composite lumber for outdoor decking. Recycled plastic is also used to create new packaging and products to be resold to consumers.