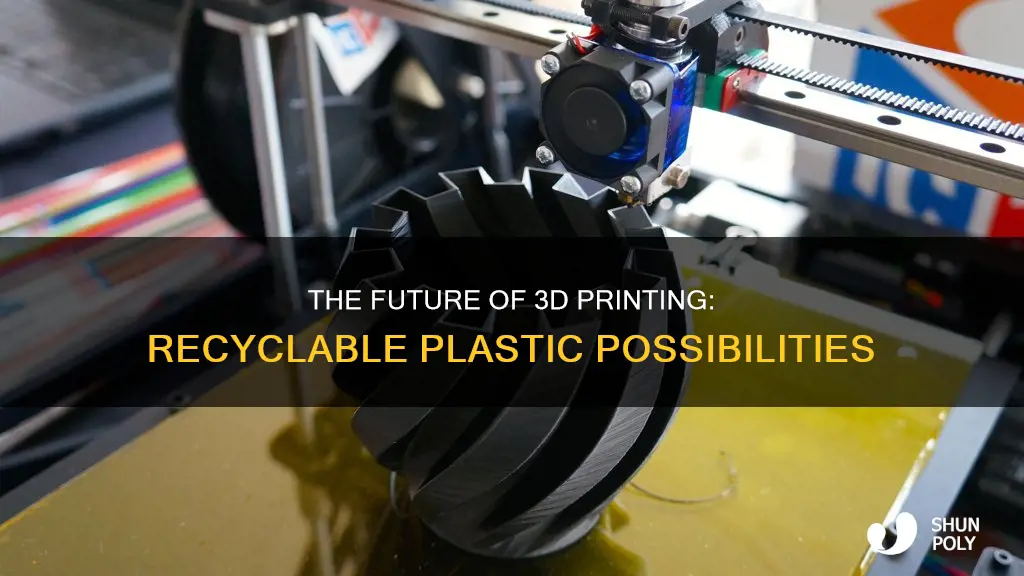
The environmental impact of 3D printing is a growing concern, with failed 3D prints accounting for more than 80% of 3D printing waste. While it is technically possible to recycle 3D-printed plastic, the process is not as simple as putting waste into a recycling bin. The two main ways to recycle 3D-printed parts are to turn the plastic back into material that can be reused for 3D printing or to use the recycled plastic for other manufacturing processes. However, the low weight-to-volume ratio of plastic makes its collection and transport costly and inefficient, and many recycling plants are unable to identify, sort, or match 3D-printed plastic with like material.
Is 3D-Printed Plastic Recyclable?
Characteristics | Values |
---|---|
Recyclability | Technically, 3D-printed plastic is recyclable, but it is not always recycled in practice due to various challenges and limitations. |
Recycling Process | 3D-printed plastic can be recycled by melting it down and reprocessing it into pellets or new filament. However, this process requires specialized equipment and is not as simple as putting it in a recycling bin. |
Recycling Challenges | The recycling process for 3D-printed plastic introduces significant quality control challenges, as recycled plastic experiences degradation in mechanical properties after a few recycling cycles. |
Environmental Impact | 3D printing contributes to plastic pollution, and proper disposal, reuse, and recycling of 3D-printed materials are essential to reduce environmental impact. |
Types of Recyclable Plastic | Common 3D-printed plastics like PLA, ABS, and PETG are classified as Type 7 plastics, which are not widely accepted or processed by local recycling centers. |
Alternative Recycling Methods | Some alternative methods for recycling 3D-printed plastic include using a homemade filament extruder, recycling into building blocks (ecobricks), or sending scraps to specialist recycling centers or material recovery facilities |
Design Considerations | Intelligent design can help reduce material waste in 3D printing, such as eliminating supports or designing them into the part itself. |
Industry Initiatives | Companies like HP and Ford Motor Company are collaborating to recycle 3D-printed waste into vehicle parts, showcasing the potential for recycled plastic in manufacturing. |
Limitations and Concerns | The low weight-to-volume ratio of plastic makes its collection and transport costly and inefficient, and there are logistical and financial challenges associated with sorting, reprocessing, and administering recycled materials. |
What You'll Learn
The two ways to recycle 3D-printed parts
3D printing plays a role in the global issue of plastic pollution. It is important that 3D printing materials are properly disposed of, reused, and recycled. While 3D-printed parts can be technically recycled, the process is not as simple as putting waste into the recycling bin for collection by the local recycling center.
There are two main ways to recycle 3D-printed parts:
- Recycling into 3D printing materials: The first way is to turn the plastic back into material that can be reused for 3D printing. This can be done by melting down the plastic waste and reprocessing it as pellets or new filament. This process can be done at home using a filament extruder, which is a machine that melts raw plastic pellets and extrudes the thermoplastic as a filament. However, recycling filament at home can lead to lower-quality materials if not done correctly, increasing the risk of part warping.
- Recycling into manufacturing materials: The second way is to use the recycled plastic to make objects used in other manufacturing processes, such as injection molding. For example, HP and the Ford Motor Company, together with SmileDirectClub and resin producer Lavergne, have been recycling 3D printer waste into low-volume vehicle parts. This involves transforming dental aligner molds into high-quality recycled plastic pellets, which can then be used for injection molding of fuel-line clips.
The extent to which 3D-printed parts can be recycled depends on the type of 3D printing used. 3D printer filaments, including nylon and polycarbonate, are typically classified as Type 7 or "Other" and are not usually recycled by municipal programs. However, some materials such as polypropylene (PP) are recycled in certain municipalities. It is important to check with local materials recovery facilities to determine if they accept 3D-printed objects for recycling.
To facilitate the recycling process, it is recommended to use a Resin Identification Code (RIC) to mark 3D-printed parts containing recyclable filaments. This code, seen inside a triangle on plastic products, helps identify different types of plastic and enables proper collection and recycling.
Additionally, it is worth mentioning that some creative ways to recycle 3D-printed scraps include reusing them in new projects, repairing broken prints, assembling multiple pieces, or donating them.
Recycling Plastic Cabinets: A Step-by-Step Guide
You may want to see also
How to recycle 3D-printed plastic at home
3D printing technology has an environmental impact as it consumes plastic and generates waste. However, there are ways to make the process more sustainable by properly disposing of, reusing, and recycling 3D printing materials.
The first step in recycling 3D-printed plastic at home is to identify the type of plastic you are dealing with. Common 3D printing plastics include PLA, ABS, PETG, and nylon. These plastics have different properties and require different recycling methods.
Once you have identified the type of plastic, you can begin the recycling process. One method is to use a filament extruder, which is a machine that melts raw plastic pellets and extrudes them into a filament. You can build your own filament extruder or purchase one online. If you plan to use failed prototypes and support materials as raw materials, you will need a plastic shredder to turn the parts into pellets that can be processed by the extruder. This method allows you to transform your 3D printer waste into new filament, reducing waste and saving money. However, it is important to note that recycling filament at home can lead to lower-quality materials if not done correctly, increasing the risk of part warping.
Another method for recycling 3D-printed plastic at home is to grind or shred the plastic into small granules or filament shavings, which can then be melted into a block or molded into a new object. This process may require an oven or a mold, depending on the type of plastic and the desired outcome.
It is important to note that some types of plastic, such as PLA, are biodegradable. However, this does not mean that they will decompose quickly in a landfill. Proper end-of-life handling is required to ensure the environmental benefits of biodegradable plastics are realized.
Starting a Paper and Plastic Recycling Business: A Beginner's Guide
You may want to see also
The challenges of recycling 3D-printed plastic
3D printing plays a role in the global issue of plastic pollution. While it is technically possible to recycle 3D-printed plastic, the process is challenging and often requires specialist equipment. The challenges of recycling 3D-printed plastic include:
Identification and Sorting
City recycling plants are unable to identify, sort, and match 3D-printed plastic with similar materials. For example, PETG, a common 3D-printed plastic, cannot be distinguished from PET (the type of plastic used in most plastic bottles) at most recycling centres, leading to contamination of the PET batch.
Quality Control
Recycling 3D-printed plastic introduces significant quality control challenges. Research indicates that the most common 3D-printing material, PLA, experiences degradation in mechanical properties after just three recycling cycles. While adding virgin polymer can mitigate these effects, it would also dilute the environmental benefits of recycling by increasing the need for new, non-recycled material per cycle.
Cost and Efficiency
The low weight-to-volume ratio of plastic makes its collection and transport costly and inefficient. Sorting, reprocessing, manufacturing, and administration also add significant financial burdens. The economics of external processing and the need to pass costs onto consumers remain complex, with virgin resin being much cheaper than recyclate.
Accessibility of Facilities
There is a lack of access to proper disposal facilities for certain types of 3D-printed plastic, such as PLA, which requires industrial composting conditions for biodegradability. This, coupled with the fact that most municipal and community recycling centres do not process Type 7 plastics (which include common 3D-printed plastics like PLA and ABS), creates challenges for individuals and companies looking to recycle 3D-printed waste responsibly.
Black Plastic: Smart Ways to Recycle
You may want to see also
The environmental impact of 3D printing
3D printing has the potential to significantly reduce environmental harm in the manufacturing process. Firstly, it reduces the need for transportation and logistics, which have a high carbon footprint. By providing versatile point-of-need fabrication, 3D printing cuts out the need for multiple carbon-intensive steps in the supply chain. This also creates operational efficiency, as products can be produced from digital files rather than being reliant on shipping.
Secondly, 3D printing can lower waste, energy usage, and the need for space. The process of additive manufacturing has a lower carbon footprint compared to subtractive processes, as it leads to less waste. Manufacturers can produce only what is needed, and hollow infill structures further cut down on material usage. In addition, 3D printing can use recycled materials, with up to 95% of the material coming from recycled sources. This could provide a solution to the problem of global waste.
However, there are also negative environmental impacts associated with 3D printing. The process can cause high levels of energy consumption, and certain materials require higher temperatures, which increases energy usage. Longer printing times and higher-quality prints also increase energy consumption. In addition, the plastic used in 3D printing may not be easily recyclable. Some types of plastic can be recycled, but this requires specialist equipment, and some types of plastic cannot be recycled at all. The difficulty of recycling 3D-printed plastic means that it often ends up in landfills, contributing to plastic pollution.
Overall, 3D printing has the potential to reduce environmental harm, but it is not yet a major solution to environmental issues. The sustainability benefits of 3D printing also need to be balanced against the potential dangers of the materials used and the proper disposal of waste.
Recycling ABS Plastic: A Comprehensive Guide
You may want to see also
The future of 3D-printed plastic recycling
3D printing is a promising manufacturing method that plays a role in the global issue of plastic pollution. While 3D printing technology consumes plastic materials, it also has the potential to reduce plastic waste and promote environmental sustainability.
Currently, there are two main ways to recycle 3D-printed parts: reusing the plastic for 3D printing or utilizing it in other manufacturing processes like injection molding. However, the recycling process is complex, and the majority of municipal recycling centers do not accept common 3D printing plastics like PLA, ABS, and PETG, classified as Type 7 plastics. This results in recyclable 3D-printed parts often being unmarked and ending up in landfills.
To address this issue, individuals can locate specialist recycling centers that process Type 7 materials or bring their waste to local maker spaces or material recovery facilities. Additionally, home recycling methods, such as using a filament extruder to melt and repurpose plastic waste, are gaining popularity. However, improper home recycling can lead to lower-quality materials and warping issues.
Looking ahead, research and development should focus on improving the strength and durability of recycled polymers, reducing their vulnerability to factors like UV light, and enhancing their environmental sustainability. By addressing these challenges, the 3D printing industry can move towards a more sustainable and circular future, minimizing plastic waste and maximizing the reuse of recycled materials.
Sorting Plastics for Recycling: A Guide to Getting it Right
You may want to see also
Frequently asked questions
Yes, 3D-printed plastic can be recycled, but it is not as simple as putting it in your recycling bin at home.
Most municipal recycling plants cannot identify, sort, or match 3D-printed plastic with like materials. The two most popular 3D printer filaments, ABS and PLA, are classified as Type 7 plastics, which are not widely accepted by local recycling centres.
You can recycle 3D-printed plastic by bringing it to a specialist recycling centre that processes Type 7 materials. Some local maker spaces or 3D printing labs also collect scraps to be sent to dedicated recycling plants. Alternatively, you can bring your leftover plastic filament and scraps to a material recovery facility, which sorts recyclable plastics and sells them to manufacturers.
Yes, you can recycle 3D-printed plastic at home using a filament extruder, which melts raw plastic pellets and extrudes the thermoplastic as a filament. You may also need a plastic shredder to turn parts into pellets that can be processed by the extruder system. However, recycling filament at home can lead to lower-quality materials if not done correctly, increasing the risk of part warping.
The logistical challenges of recycling 3D-printed plastic are considerable. The low weight-to-volume ratio of plastic makes its collection and transport costly and inefficient. Sorting, reprocessing, manufacturing, and administration also add significant financial burdens. Additionally, there is a lack of widespread access to proper disposal facilities for certain types of 3D-printed plastic, such as PLA, which requires industrial composting conditions for biodegradability.