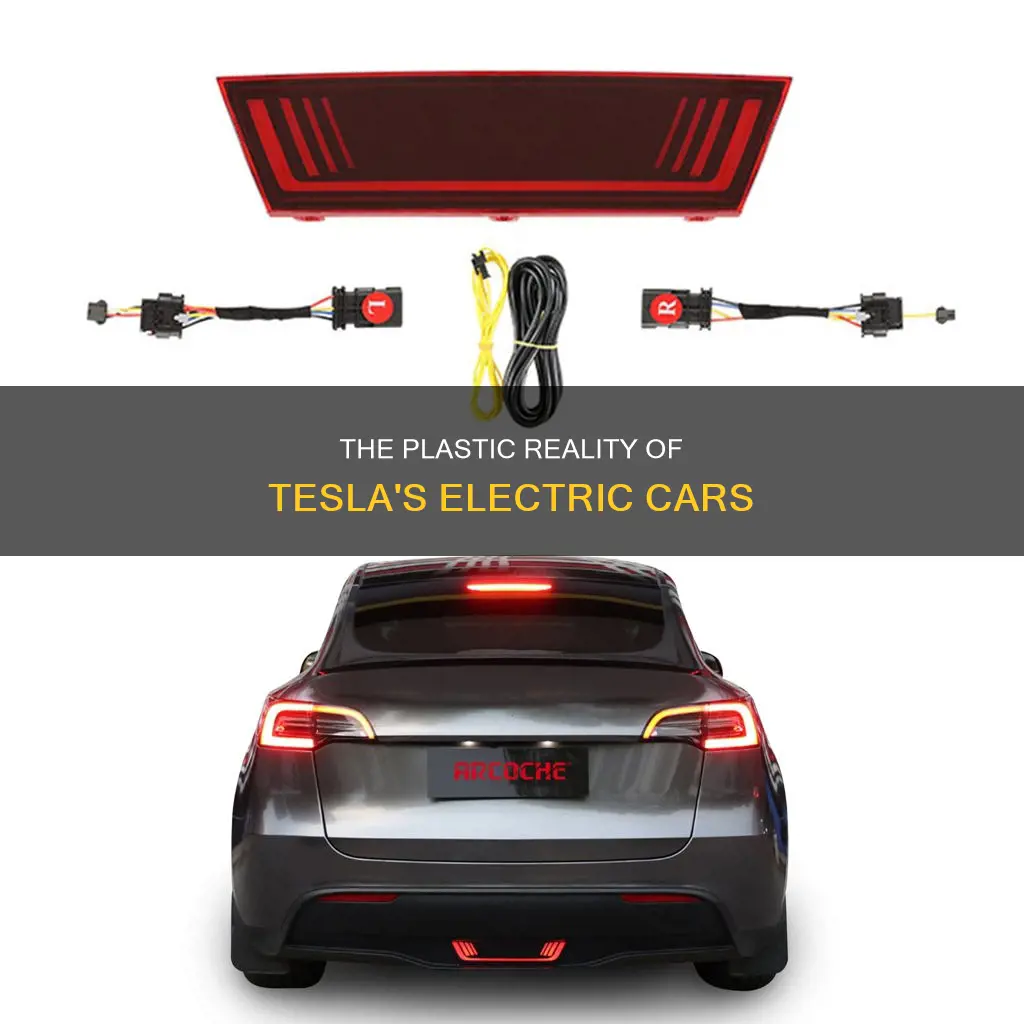
Tesla is well-known for its auto-pilot cars and huge investments in batteries, but it is also making developments in plastics. Tesla's manufacturing unit in Nevada, also called Giga Nevada or Gigafactory 1, uses plastic in making battery casing, separators, solar polymer cells, and autonomous indoor vehicles. The company is also researching methodologies for improving the recyclability of plastics and other organic materials.
Characteristics | Values |
---|---|
Plastic in electric vehicles market estimated value in 2021 | $943.01m |
Plastic in electric vehicles market CAGR | 37.3% |
Plastic used in making battery casing, separators, solar polymer cells, autonomous indoor vehicles | Lithium-ion batteries |
Plastic recycling | Tesla is researching methodologies for improving recyclability of plastics |
What You'll Learn
- Tesla's use of plastic in battery casing, separators, solar polymer cells, and autonomous indoor vehicles
- Tesla's research into improving the recyclability of plastics
- Tesla's use of carbon fibre encapsulated in epoxy resin
- Tesla's suppliers of plastic components
- The global plastic in electric vehicles market
Tesla's use of plastic in battery casing, separators, solar polymer cells, and autonomous indoor vehicles
Tesla has been making developments in plastics for the past 20 years, with a focus on improving the recyclability of plastics and other organic materials. In 2019, Tesla sent 1000 tons of nickel, 320 tons of copper and 110 tons of cobalt for recycling.
Tesla's manufacturing unit in Nevada, also called Giga Nevada or Gigafactory 1, is largely focused on making lithium-ion batteries. Plastics are used in the battery casing, separators, solar polymer cells, and autonomous indoor vehicles.
Tesla has been recycling about 90% of its lead-acid batteries, which form 60-70% of the new manufactured batteries. The global plastic in electric vehicles market is estimated to grow with a CAGR of 37.3% during the forecast period and will reach $943.01 million by 2021.
Plastic Pollution: America's Garbage Crisis
You may want to see also
Tesla's research into improving the recyclability of plastics
Tesla is researching methodologies for improving the recyclability of plastics and other organic materials. The company has been recycling about 90% of its lead-acid batteries, which form 60-70% of new manufactured batteries.
Tesla's manufacturing unit in Nevada, also called Giga Nevada or Gigafactory 1, is largely into the making of lithium-ion batteries, wherein plastics are used in making battery casing, separators, solar polymer cells, and autonomous indoor vehicles.
The global plastic in electric vehicles market is estimated to grow with a CAGR of 37.3% during the forecast period and will reach $943.01 million by 2021. Continued inputs by the government in terms of investments in plastic production and support by way of encouraging regulations are likely to contribute to the growth of this market.
Tesla is well-known for its auto-pilot cars and huge investments in batteries, but it is also making developments in plastics. The company has five large factories in California, Tilburg, Nevada, New York, and Shanghai, and two plants under construction in Brandenburg and Texas.
Plastic Pipe Cost: A Comprehensive Guide to Pricing
You may want to see also
Tesla's use of carbon fibre encapsulated in epoxy resin
Tesla is well-known for its auto-pilot cars and huge investments in batteries, but it is also making developments in plastics. The company has been recycling about 90% of its lead-acid batteries for the past 20 years, which form 60-70% of the new manufactured batteries.
Tesla's manufacturing unit in Nevada, also called Giga Nevada or Gigafactory 1, is largely into the making of lithium-ion batteries. Plastics are used in making battery casing, separators, solar polymer cells, and autonomous indoor vehicles.
The skin of the Tesla Roadster is made using carbon fibre encapsulated in epoxy resin, using the process of resin transfer moulding. The material was also used in its rear panel. Carbon fibres are long, thin strands of pure carbon that are strong in tension (when pulled) and are reasonably flexible. The strands are tightly woven in a cloth and then encapsulated in plastic or resin. The resulting material is lightweight but extremely strong and durable – the perfect skin for the Tesla Roadster.
Carbon fibre on its own isn’t much use. It’s like a very thin fishing line, it is only strong in tension (when you try to break it by pulling it along its length). So, to make a panel that is strong in all directions, carbon fibre is typically woven into cloth (to give it strength in two directions) and then the carbon fibre cloth is encapsulated in epoxy resin. The epoxy is strong in compression but relatively weak in tension, so the two materials act together to produce a panel strong in tension and compression.
The Weight of Plastic Wrap: How Much?
You may want to see also
Tesla's suppliers of plastic components
Tesla uses plastic in the making of battery casing, separators, solar polymer cells, and autonomous indoor vehicles.
Plastikon Industries, a plastic parts manufacturer, is one of Tesla's suppliers. Plastikon has leased nearly 100,000 square feet in the Plum Creek Industrial Center in the suburb of Kyle, about 30 minutes from Tesla’s rising gigafactory.
In 2015, Tesla was in talks with its metal and plastic parts supplier Riviera Tools LLC to accommodate the supply of parts during the production ramping up of its luxury Model S cars. The company was later renamed as Tesla Tool and Die Factory.
Nova company is responsible for many of the plastic-moulded Tesla parts. They have supplied thousands of auto parts to manufacturers all over the world.
Saueressig Engineering, a division of Pittsburg-based Matthews International Corp., is another reported Tesla supplier. The company designs, manufactures and services custom equipment including lithium-ion battery electrodes.
Large Plastic Toy Horses: How Much Do They Cost?
You may want to see also
The global plastic in electric vehicles market
Tesla is well-known for its auto-pilot cars and huge investments in batteries, but it is also making developments in plastics. The company has been recycling about 90% of its lead-acid batteries for the past 20 years, which form 60-70% of the new manufactured batteries. Tesla's manufacturing unit in Nevada, also called Giga Nevada or Gigafactory 1, is largely into the making of lithium-ion batteries, where plastics are used in making battery casing, separators, solar polymer cells, and autonomous indoor vehicles.
Plastic Recycling Machine Costs: A Comprehensive Overview
You may want to see also
Frequently asked questions
Tesla uses plastic in the making of battery casing, separators, solar polymer cells, and autonomous indoor vehicles.
Tesla has been recycling about 90% of its lead-acid batteries for the past 20 years, which form 60-70% of new manufactured batteries. They are also researching methodologies for improving the recyclability of plastics and other organic materials.
As per Tesla's 2019 Impact Report, Tesla sent 1000 tons of nickel, 320 tons of copper, and 110 tons of cobalt for recycling.