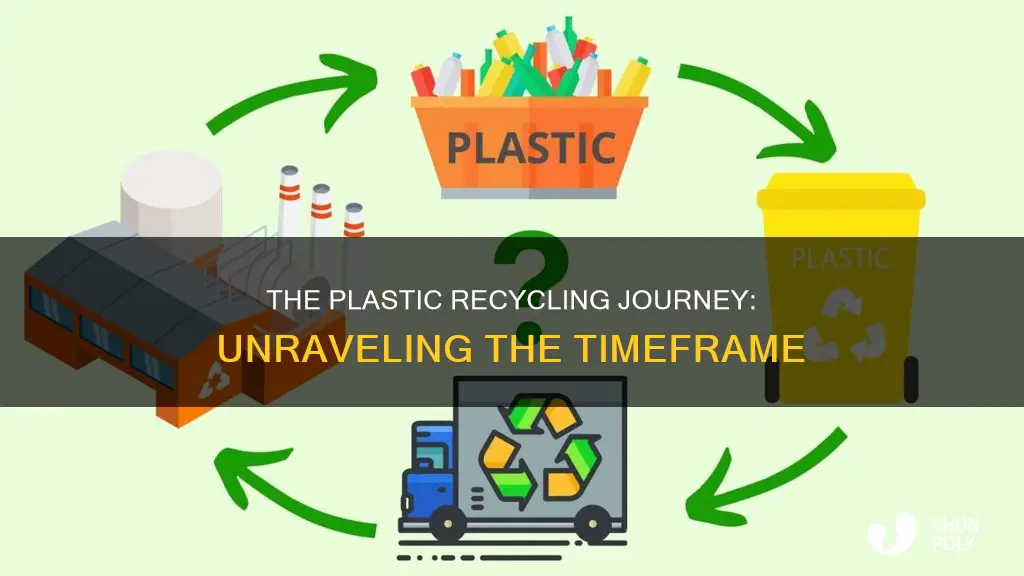
The process of recycling plastic is a complex journey, and understanding its duration is crucial for effective waste management. Plastic recycling involves transforming used plastic materials into new products, but the time it takes for this transformation varies significantly. From the moment plastic waste is collected, it can take anywhere from a few weeks to several months, or even longer, to be fully recycled and reborn as a new item. This duration is influenced by various factors, including the type of plastic, the recycling method, and the efficiency of the recycling facility. In this exploration, we will delve into the factors that determine the timeline of plastic recycling and its impact on the environment.
What You'll Learn
Collection and Sorting: Plastic waste is collected and sorted by type
The process of recycling plastic begins with the crucial step of collection and sorting, which is a fundamental phase in ensuring the efficiency and effectiveness of the recycling process. Plastic waste is collected from various sources, including residential areas, commercial establishments, and public spaces, through organized recycling programs or waste management systems. This initial step is vital as it sets the foundation for the entire recycling journey. Once collected, the plastic waste undergoes a meticulous sorting process, which is a critical aspect of recycling.
Sorting plastic waste by type is essential because different types of plastics have unique chemical compositions and properties, and they require specific recycling methods. Common types of plastics include PET (polyethylene terephthalate), HDPE (high-density polyethylene), PVC (polyvinyl chloride), LDPE (low-density polyethylene), and PP (polypropylene). Each type has its own recycling challenges and applications. For instance, PET is widely used in beverage bottles and can be recycled into fibers for clothing or new bottles. HDPE, commonly found in milk jugs and shampoo bottles, is durable and can be recycled into items like outdoor furniture and trash cans. PVC, often used in construction and plumbing, requires careful handling due to its hazardous nature. LDPE and PP, while less common in packaging, have their own recycling pathways.
The sorting process typically involves manual labor and advanced machinery. Manual sorting is often done in recycling centers where workers carefully separate the plastics based on their colors, textures, and types. This human-led approach ensures accuracy and allows for the identification of any contaminants. Advanced machinery, such as optical sorters and eddy current separators, is also employed to streamline the process. Optical sorters use light to identify different plastics based on their color and transparency, while eddy current separators detect the conductivity of materials, separating metals and non-metals. These technologies enhance efficiency and reduce the risk of human error.
After sorting, the plastic waste is further categorized into clean and contaminated streams. Clean plastics are those that have been properly sorted and are free from food residue, labels, and other contaminants. These clean plastics are then ready for processing into new products. Contaminated plastics, on the other hand, contain items like food waste, labels, or other non-plastic materials and require additional cleaning and processing. This separation ensures that the recycling process is more effective and reduces the likelihood of contamination in the final recycled products.
In summary, the collection and sorting of plastic waste is a critical and intricate process that forms the basis of successful plastic recycling. It requires a combination of organized collection systems, manual labor, and advanced technology to separate plastics by type and condition. This step is essential to ensure that the subsequent recycling processes are efficient, cost-effective, and environmentally friendly, ultimately contributing to a more sustainable approach to managing plastic waste.
Unveiling the Secrets: How Recycling Plants Sort Plastic Bottles
You may want to see also
Cleaning: Materials are cleaned to remove contaminants
The cleaning process is a crucial step in plastic recycling, as it ensures that the materials are free from contaminants and ready for further processing. This step is essential to maintain the quality and integrity of the recycled plastic, as any remaining impurities can affect the final product's performance and durability. Here's a detailed breakdown of the cleaning process:
Sorting and Separation: The first part of cleaning involves sorting and separating different types of plastics. Plastic recycling facilities use various methods to identify and categorize plastics based on their resin identification codes (RICs). Common types include PET (polyethylene terephthalate), HDPE (high-density polyethylene), LDPE (low-density polyethylene), and PP (polypropylene). This initial sorting is often done manually or with the help of automated systems, ensuring that similar plastics are grouped together.
Physical Cleaning: After sorting, the plastic materials undergo physical cleaning to remove any visible contaminants. This process typically includes washing the plastics with water to eliminate dirt, labels, and other non-plastic components. Advanced recycling facilities might use specialized washing machines that employ high-pressure water jets and mechanical brushes to ensure thorough cleaning. The washed plastics are then dried to remove excess moisture, which is crucial for the next stage.
Chemical Cleaning: For more effective contamination removal, chemical cleaning is employed. This process involves using specific chemicals to dissolve or break down contaminants. For instance, oils and greases can be removed using organic solvents, while more stubborn contaminants like food residues might require stronger acids or bases. Chemical cleaning is carefully monitored to ensure that the chemicals used do not damage the plastic itself. After treatment, the plastics are thoroughly rinsed to eliminate any residual chemicals.
Advanced Cleaning Techniques: In some cases, more advanced cleaning methods are utilized. These include the use of ultrasonic baths, which employ high-frequency sound waves to dislodge contaminants from the plastic surface. Another technique is air-knife drying, where a stream of air is used to remove moisture and any remaining contaminants. These methods are particularly useful for removing fine particles and ensuring a high level of cleanliness.
Quality Control: Throughout the cleaning process, quality control checks are performed to ensure that the materials meet the required standards. This includes visual inspections, weight measurements, and sometimes, more advanced testing methods to verify the absence of contaminants. The cleaned plastics are then ready for the next stage of recycling, where they will be transformed into new products, contributing to a more sustainable and circular economy.
Transforming Recycled Plastic: A Journey from Waste to Warrior Gear
You may want to see also
Shredding/Grinding: Plastic is shredded or ground into small pieces
The process of recycling plastic begins with shredding or grinding the plastic materials into small, manageable pieces. This initial step is crucial as it prepares the plastic for further processing and ensures that it can be effectively sorted and cleaned. When plastic is shredded, it is typically fed into a specialized machine that uses sharp blades or a rotating drum to cut the plastic into tiny fragments. This process can vary in intensity, with some machines capable of producing very fine particles, while others create larger, more substantial pieces. The shredded plastic is then sorted based on its type and color, which is essential for maintaining the quality of the recycled material.
Grinding, on the other hand, often involves using a mechanical grinder to reduce the plastic into even smaller particles. This method is particularly useful for creating a consistent and uniform size of plastic flakes, which can be further processed into various recycled products. The grinding process can be customized to achieve different particle sizes, depending on the intended application of the recycled plastic. For instance, finer particles might be used for creating new plastic pellets, while coarser ones could be suitable for manufacturing plastic lumber or other composite materials.
Both shredding and grinding techniques are designed to minimize the volume of plastic waste while maximizing its potential for reuse. By reducing the size of the plastic, these processes increase the surface area, allowing for more efficient cleaning and separation of contaminants. This step is critical in ensuring that the recycled plastic meets the required standards and can be used in various industries, from manufacturing new products to creating innovative solutions for waste management.
The shredded or ground plastic is then typically washed to remove any remaining contaminants, such as labels, dirt, or other non-plastic materials. This washing process helps to ensure that the recycled plastic is clean and free from impurities, which is essential for maintaining its quality and value. After washing, the plastic flakes are often dried to remove any excess moisture, making them ready for the next stage of recycling.
In summary, shredding and grinding are fundamental processes in plastic recycling, transforming large plastic items into small, uniform pieces. These methods not only reduce the volume of waste but also prepare the plastic for further processing, ensuring that it can be effectively recycled and reused in various applications, contributing to a more sustainable and circular economy.
Chopping Board Eco-Friendly: Can Plastic Chopping Boards Be Recycled?
You may want to see also
Melting: The plastic is melted and formed into pellets
The process of recycling plastic involves several stages, and one crucial step is the melting phase, where plastic is transformed into a usable form. This process begins with the collection and sorting of plastic waste, ensuring that different types of plastics are separated to facilitate the recycling process. Once sorted, the plastic is prepared for melting, which is a critical step in recycling.
Melting involves heating the plastic to its glass transition temperature, which varies depending on the type of plastic. For example, high-density polyethylene (HDPE) typically requires temperatures around 230°C (446°F), while polypropylene (PP) needs slightly higher temperatures of around 160°C (320°F). The plastic is fed into a melting machine, where it is heated and softened, allowing it to be shaped and molded. This step requires precise control of temperature and time to ensure the plastic is melted thoroughly but not burned or degraded.
During the melting process, the plastic is often shredded or granulated to create a consistent and uniform material. This step is crucial as it prepares the plastic for the next phase, where it is formed into pellets. The shredded or granulated plastic is then cooled and extruded through a die to create small, uniform pellets. These pellets are the raw material for manufacturing new products, as they can be easily molded, shaped, and processed into various items.
The formation of pellets is a critical stage in the recycling process, as it ensures the plastic is in a usable form. These pellets are then sold to manufacturers who use them to produce new products, such as toys, furniture, and even new packaging. The entire recycling process, from collection to melting and pellet formation, can take several weeks to months, depending on various factors, including the recycling facility's capacity, the type of plastic, and the demand for recycled materials.
In summary, the melting process is a vital step in recycling plastic, where it is transformed into a usable form through precise heating and shaping. This phase, along with the subsequent pellet formation, ensures that plastic waste can be effectively recycled and reused, contributing to a more sustainable and circular economy. Understanding these processes is essential to appreciating the complexity and time investment required in recycling plastic materials.
Unraveling the Process: How PP Plastic is Recycled
You may want to see also
Reuse: Pellets are used to create new products
The process of recycling plastic and transforming it into new products is a fascinating journey, and one of the most crucial steps is the reuse phase, where plastic pellets play a vital role. After plastic waste is collected, sorted, and processed, it is often shredded into small pieces, a process known as granulation. These plastic flakes are then washed to remove any contaminants and dried to ensure they are ready for the next stage. The dried flakes are fed into a machine that melts and extrudes them into long strands, which are then cut into small, uniform pellets. These pellets are the raw material for creating new products.
These plastic pellets, often referred to as 'nurdles' in the industry, are incredibly versatile. They can be used to manufacture a wide range of products, from everyday household items to industrial machinery. The process of creating new products from these pellets involves heating and shaping them. Manufacturers can mold, inject, or blow-mold these pellets to form various shapes and sizes, depending on the desired product. For example, they can be used to produce new plastic bottles, containers, packaging materials, and even construction materials like pipes and profiles.
The beauty of this reuse process is its sustainability. By reusing plastic pellets, we can significantly reduce the demand for virgin plastic production, which often relies on fossil fuels and non-renewable resources. This not only helps conserve natural resources but also reduces the environmental impact associated with the extraction and processing of raw materials. Additionally, the production of new products from recycled plastic pellets can create a closed-loop system, minimizing waste and promoting a circular economy.
The applications of recycled plastic pellets are vast and diverse. In the consumer goods sector, they can be used to create lightweight, durable packaging materials, ensuring products remain fresh and protected during transportation and storage. In the automotive industry, recycled plastic is utilized for interior components, dashboards, and even car exteriors, contributing to a more sustainable and eco-friendly approach to vehicle manufacturing. Furthermore, the construction industry benefits from recycled plastic pellets, as they can be transformed into insulation materials, pipes, and even paving blocks, offering a more environmentally conscious alternative to traditional building materials.
In summary, the reuse of plastic pellets is a critical step in the recycling process, allowing us to give new life to old plastic waste. Through this method, we can create a wide array of products, from everyday items to specialized industrial components. Embracing this practice not only reduces environmental impact but also fosters a more sustainable and circular approach to manufacturing, ensuring a greener future for generations to come.
Black Plastic DVD Cases: Can They Be Recycled?
You may want to see also
Frequently asked questions
The recycling process for plastic can vary significantly depending on several factors, including the type of plastic, the recycling method, and the specific recycling facility. On average, it can take anywhere from a few weeks to several months for plastic to be recycled and transformed into a new product. For instance, PET (polyethylene terephthalate), commonly used in beverage bottles, can be recycled and turned into new bottles within a few months. However, HDPE (high-density polyethylene), often used for milk jugs, can take longer, sometimes up to a year, due to the complexity of the recycling process.
Yes, several measures can be taken to expedite the recycling process. Advanced recycling technologies, such as chemical recycling, can break down plastic into its original building blocks, allowing for the creation of new products more efficiently. Additionally, improving the collection and sorting processes can significantly reduce the time it takes for plastic to be recycled. Implementing better waste management systems and encouraging consumer participation in recycling programs can also contribute to faster recycling rates.
One of the primary challenges in plastic recycling is the contamination of plastic waste with food residue, labels, and other non-plastic materials. This contamination can render the plastic unusable for certain applications. To address this, public awareness campaigns can educate consumers about proper waste segregation. Additionally, investing in advanced sorting technologies can help separate different types of plastics more effectively. Another challenge is the lack of standardized recycling processes, which can vary widely across regions. Standardization and collaboration between recycling facilities, manufacturers, and policymakers are essential to streamline the recycling process and reduce the time it takes for plastic to be recycled.